Si chiama “Omega 1 Turbine” ed è un propulsore di nuova concezione sviluppato dalla startup americana Astron Aerospace che ridefinisce il concetto di motore rotativo con soluzioni che si ispirano alle turbine a gas. Obiettivi del progetto raggiungere un’efficienza termica superiore al 60 per cento e rapporti peso potenza dell’ordine dei 100 grammi per cavallo.
Non capita tutti i giorni di assistere alla nascita di un nuovo motore a combustione interna. A maggior ragione se l’aggettivo “nuovo” non si riferisce a un motore realizzato da un costruttore di settore. Bensì da una start-up che ha operato senza condizionamenti progettuali. Proponendo un’unità nuova nell’architettura di funzionamento e nei meccanismi che governano il moto dei singoli componenti. Nel caso di “Omega 1 Turbine” ci si trova proprio al cospetto di tale evento. E sebbene l’unità sia ancora in fase di sviluppo da parte dell’azienda progettista, Astron Aerospace, le sue innovative caratteristiche e le performance dichiarate l’hanno già portata sotto le luci della ribalta. Attirando su di lei l’interesse dei più svariati ambiti industriali.
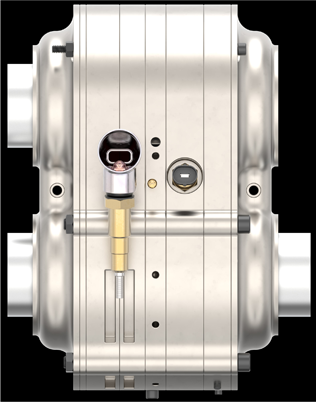
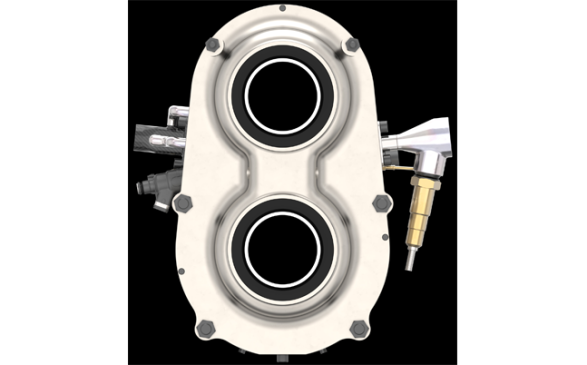
Ciò anche se le caratteristiche prestazionali non sono ancora state pienamente confermate né risultano verificate le reali sostenibilità di produzione e di industrializzazione del prodotto. L’architettura del motore e i suoi principi di funzionamento sono però troppo originali per non destare interesse. Soprattutto alla luce di processi di conversione energetica che portano l’efficienza a superare di larga misura gli standard proposti dai motori endotermici tradizionali.
Va precisato che “Omega 1 Turbine” nasce per andare incontro alle necessità propulsive del segmento aeronautico. Detto questo l’unità ben si presta per operare in qualsiasi settore oggi coperto dai motori a combustione tradizionali. Dall’automotive alle applicazioni industriali e agricole. Il motore opera in effetti sulla base un ciclo termodinamico di tipo otto. Quindi quattro tempi con alimentazione a benzina, proponendosi con un’architettura che esula dalla presenza di componenti in moto alterno e assimilandosi piuttosto alle unità rotative tipo Wankel. Con tali motori condivide infatti l’utilizzo di rotori inseriti all’interno di casse statoriche. Elementi che vanno a definire i volumi nei quali avvengono poi i processi termodinamici.
Un po’ rotativo un po’ turbina a gas
La similitudine con i Wankel però finisce qui. Divergendo completamente la struttura e il funzionamento, con quest’ultimo che, come suggerisce anche il nome dell’unità, si ispira a quello di una turbina a gas. Di fatto, una sorta di ibrido tra le turbine e i motori rotativi. Ciò in quanto le quattro fasi del ciclo di lavoro, come sulle turbine, vengono asservite da due differenti macchine termiche. O, meglio, da due macchine termiche uguali affiancate l’una all’altra.
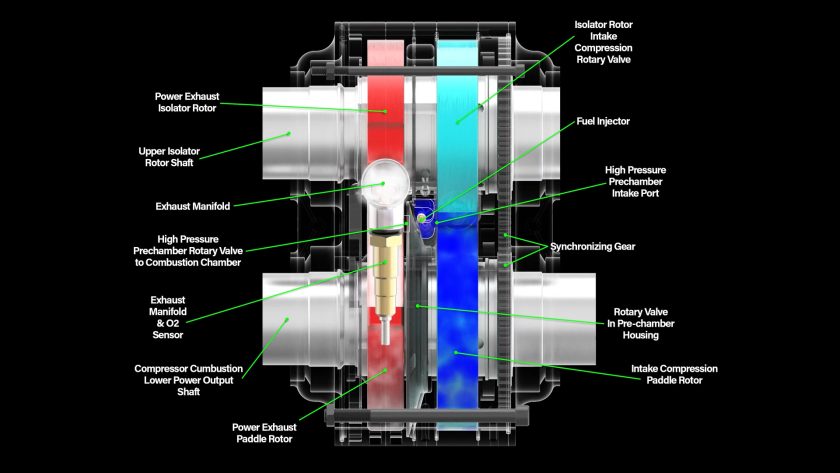
La prima, la macchina fredda, asseconda i processi di aspirazione e compressione, la seconda, la macchina calda, le fasi di espansione e scarico. Ciascuna macchina è costituita da due rotori cilindrici di diametri diversi fra loro. Sovrapposti in modo da poter ruotare l’uno sull’altro in maniera sincronizzata senza slittamenti. Obiettivo raggiunto tramite una coppia di ingranaggi ciascuno dei quali è collegato a un rotore tramite un albero motore. Lo stesso cui si collegano poi anche i rotori della seconda macchina termica.
Due gli alberi motore
Nel suo complesso l’unità vede quindi la presenza di due alberi motore. Uno per il rotore superiore e uno per il rotore inferiore. Componenti uguali fra loro e caratterizzati da un diametro di sezione maggiore rispetto agli alberi motore tradizionali essendo a sezione cava. Le superfici laterali dei rotori sono inoltre lisce. Uno si propone però con una sorta di dente che durante il funzionamento va a inserirsi in una nicchia proposta dall’altro rotore. Entrambi ruotano all’interno di casse statoriche di sezione circolare le cui pareti sono lavorate a macchina con tolleranze che oscillano tra i due e i dieci centesimi di millimetro.
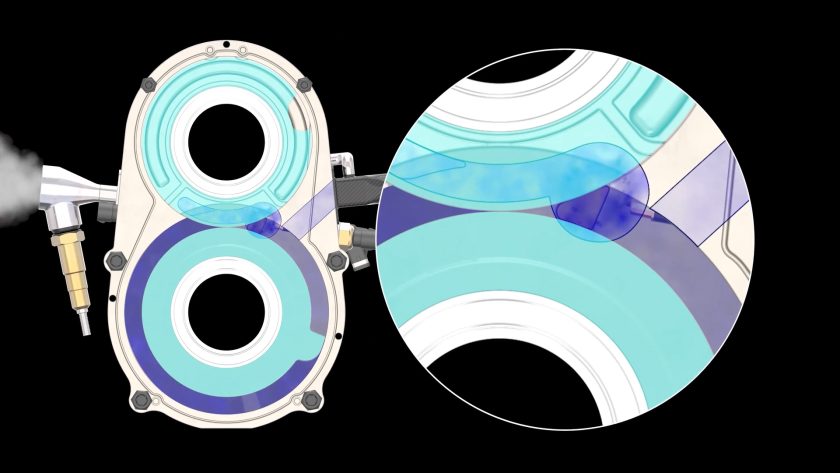
Una delle due casse vede un diametro pari a quello del rotore, mentre l’altra propone un diametro superiore per poter permettere la rotazione del dente. Ne deriva che attorno al rotore “dentato” si realizza una camera toroidale che viene continuamente attraversata dal dente durante la rotazione. Il ciclo di lavoro inizia con la fase di aspirazione, cui provvede il rotore “dentato” proposta dalla scatola fredda. Questi, ruotando, crea dietro di sé una depressione che aspira l’aria esterna e contemporaneamente spinge quella presente davanti a sé verso l’area di contatto con l’altro rotore.
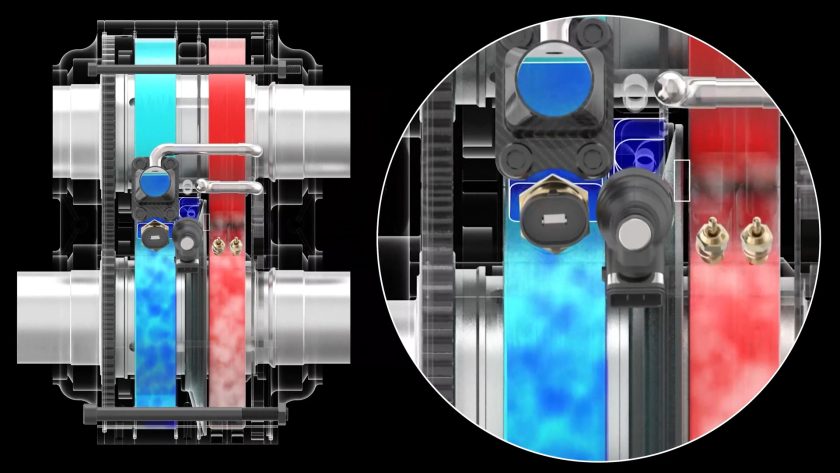
In tal modo, nel punto di contatto fra i due rotori si accumula aria compressa. Aria che passa poi in una precamera di combustione realizzata nel blocco e posizionata fra le due macchine termiche. Il passaggio è modulato dall’incavo realizzato nell’altro rotore che funge quindi da valvola. La precamera si presenta con una geometria a sezione circolare, studiata per imprimere ai gas presenti un’elevata vorticosità e quindi un energico rimescolamento. Va precisato che la pressione all’interno della camera è gestita tramite una valvola di sfogo che permette di regolarla in un range compreso tra i 12 e i 22 bar. A seconda del carico e quindi delle prestazioni richieste.
Iniezione diretta e modulabile
A tale obiettivo guarda poi anche il sistema di iniezione di tipo diretto. Operando sempre nella precamera di combustione. fornisce la carica del carburante, modulabile in base alla tipologia di quest’ultimo e al regime. Ai bassi e ai medi è infatti possibile realizzare una carica stratificata. Rendendola omogenea quando si vogliono attuare strategie di innesco di tipo “Hcci” per incrementare l’efficienza di combustione agli alti regimi limitando contemporaneamente le emissioni. L’immissione di carburante avviene inoltre poco prima che una valvola a disco rotante analoga a quelle in uso sui motori a due tempi sportivi colleghi la precamera con la macchina termica calda. Dove avviene la combustione vera e propria.
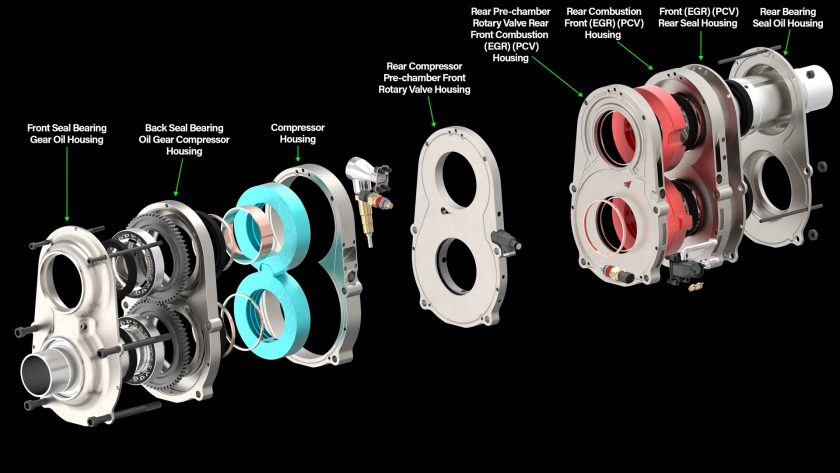
Questa si realizza nel vano statorico. In cui è presente il rotore “dentato” con la miscela che viene immessa subito dopo il passaggio del dente del rotore a ridosso di una candela di accensione. A quel punto la miscela si innesca, entra in combustione e dà luogo a un’espansione che agisce sul dente. Determinando quindi la rotazione del rotore e quindi generando energia meccanica.
L’espansione dei gas prosegue lungo l’arco del vano statorico fino a raggiungere un’area di scarico posta prima della zona in cui si incontrano dente e relativo incavo. Sul lato opposto della camera ad anello in cui avvengono combustione ed espansione. A questo punto entra in gioco la nicchia prevista sul rotore non dentato che apre il passaggio permettendo ai gas combusti di liberarsi in atmosfera.
Efficienza termica superiore al 60%
Secondo Astron Aerospace le forze di pressione opererebbero su un arco di circa 275 gradi in riferimento alla rotazione dell’albero. Godendo anche di una maggiore “leva” tra l’asse dell’albero e il punto di applicazione della forza meccanica generata dai gas grazie al superiore diametro del rotore rispetto a un perno di manovella. Sulla base di tali caratteristiche l’efficienza termica dell’unità supererebbe il 60 per cento e quella meccanica il 90 per cento.Valori che permetterebbero a un’unità da 15 chili di massa di sviluppare una potenza di oltre 160 cavalli e una coppia di 230 newtonmetro, a regimi di rotazione che oscillerebbero tra i mille e i 25 mila giri.
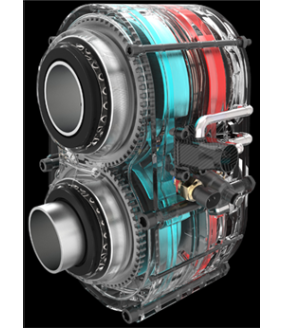
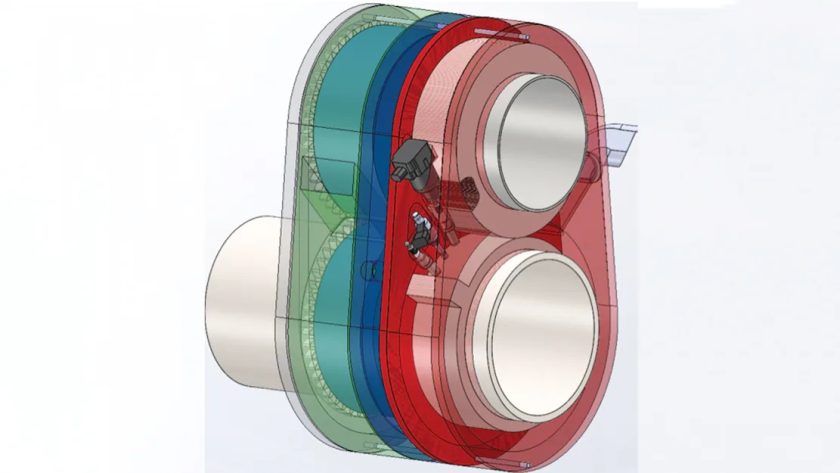
Ciò significa che in abito aeronautico, accoppiando il motore a un gruppo propulsivo a elica, si disporrebbe di un sistema lungo solo 35 centimetri, largo 38 e alto 58 in grado di erogare fino a 600 cavalli a 15 mila giri con una coppia di mille 355 newtonmetro, per un’efficienza termica dell’ottanta per cento.
Quasi nulli gli attriti interni
Questo grazie anche a una riduzione degli attriti interni dovuta all’assenza di anelli di tenuta o guarnizioni tra i componenti in rotazione, con l’unica eccezione costituita dai supporti degli alberi motore realizzati tramite cuscinetti a sfera disposti all’interno di un carter dedicato. In tale ottica la lubrificazione dell’unità sarebbe avanzata tramite olio solo su tali componenti, come nei motori a due tempi, ma escludendo la possibilità di trafilamento del fluido nei volumi di combustione e quindi abbattendo sia i consumi di olio sia quelli relativi alle emissioni inquinanti. A conferma il fatto che la startup americana dichiarato anche minori costi di manutenzione legati al cambio olio, avanzato, nel caso di un’applicazione su veicolo, ogni ottanta mila chilometri.
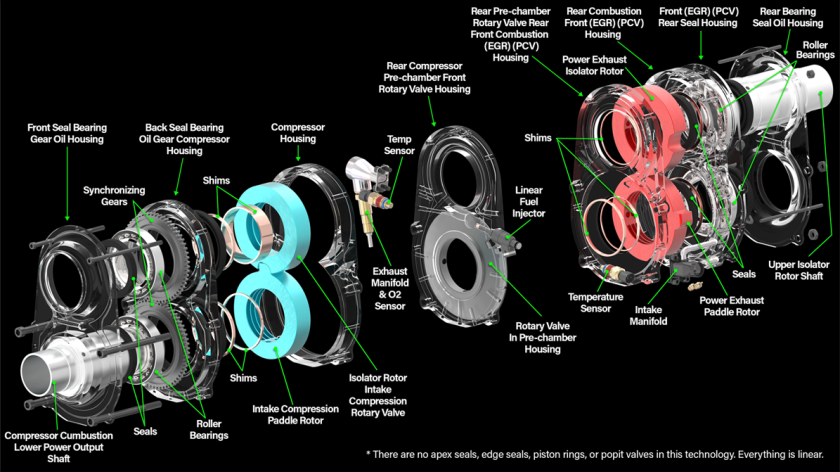
Semplificato anche il sistema di raffreddamento, ad aria con passaggio della stessa attraverso gli alberi motore che realizzano un’ampia superficie di scambio termico proprio a ridosso degli elementi più sollecitati. L’adozione di strategie di combustione a carica omogenea “Hcci” permette invece di accelerare la combustione stessa riducendo contemporaneamente la superficie della camera, cosa che a sua volta permette di contenere le emissioni degli ossidi di azoto eliminando la necessità di utilizzare catalizzatori a tre vie. L’adozione di strategie di combustione di tipo “skip-fire”, ossia escludendo l’alimentazione e quindi la combustione a intervalli, favorirebbe il funzionamento dell’unità quando opera a carichi contenuti.
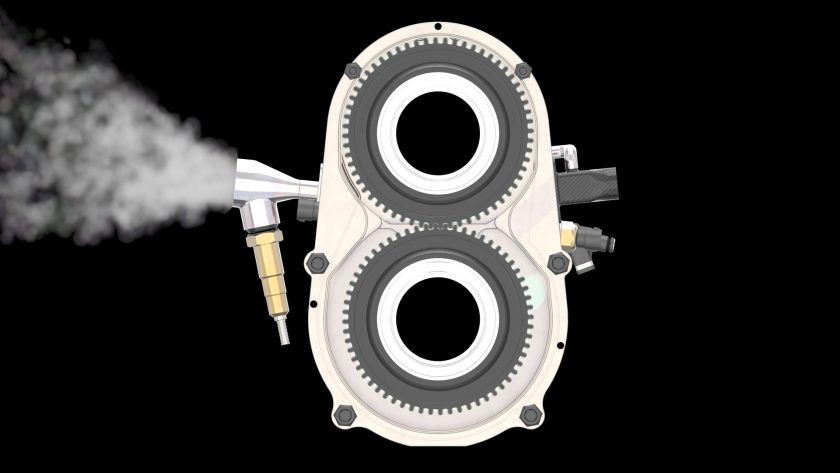
Proprio per assicurare un perfetto controllo della combustione i progettisti hanno previsto l’inserimento di una coppia di sensori di temperatura nella camera di aspirazione-compressione e a ridosso dello scarico. Sull’aspirazione è invece previsto un doppio sistema di ricircolo egr operante tramite normali valvole di controllo di pcv per far ricircolare i gas combusti sia nei condotti di aspirazione al fine di abbattere le emissioni di ossidi di azoto e per collega l’airbox al collettore di scarico permettendo di apportare ossigeno nei gas di scarico per migliorarne l’ossidazione nel catalizzatore, soprattutto quando il motore è freddo o lavora a basso carico.
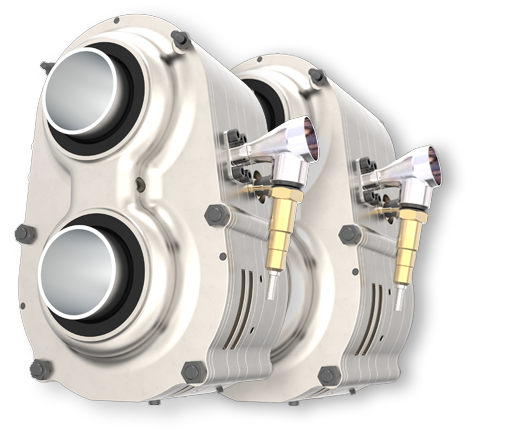
Ideale per power unit ibride
Da sottolineare infine che il layout dell’unità e i ridotti ingombri ben si prestano ad assecondarne l’integrazione su power unit di tipo ibrido. In accoppiamento a motori elettrici, incrementando ulteriormente l’efficienza del sistema. O in accoppiamenti multipli che consentono di unire più unità in serie avanzando un più facile dimensionamento prestazionale del gruppo propulsivo. Quanto fin qui scritto però non è da dimenticare che sarà da confermare una volta raggiunta la maturità del prodotto in termini di sviluppo, di affidabilità e di sostenibilità economica a livello di costi produttivi.
Rotativo Omega 1 Turbine
Autore: Jacopo Oldani