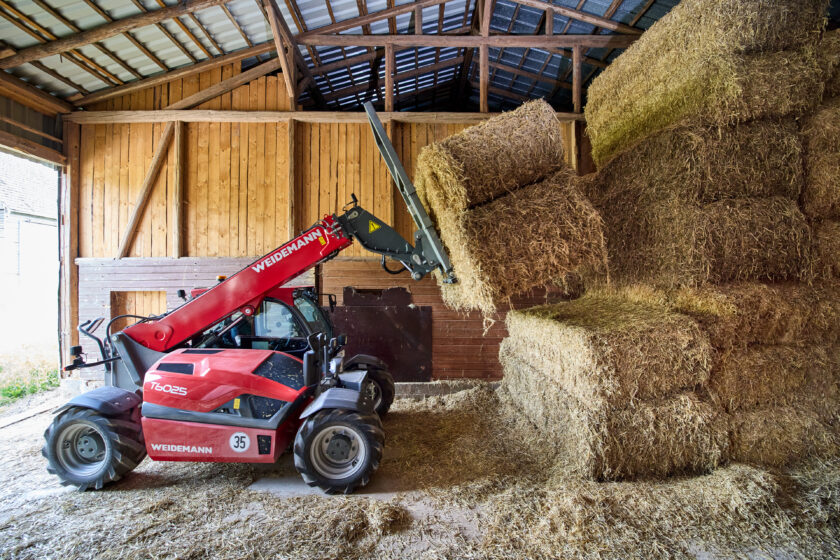
The range of Weidemann telehandlers expanded in early November with the launch of the “T6025” model, positioned between the “T7035” model and the ultra-compact “T4512,” the latter also available in an electric version. At first glance, the new machine might seem like a simple addition to fill the performance gap between the two aforementioned models in terms of capacity and height. However, it is actually another declaration of war by Weidemann against competitors, already challenged in the seven- and nine-meter height classes and now also targeting the highly popular six-meter class, particularly relevant in livestock farming and commercially attractive in agriculture in countries like Italy, where family-run farms remain prevalent.
Standard “Vertical Lift System”
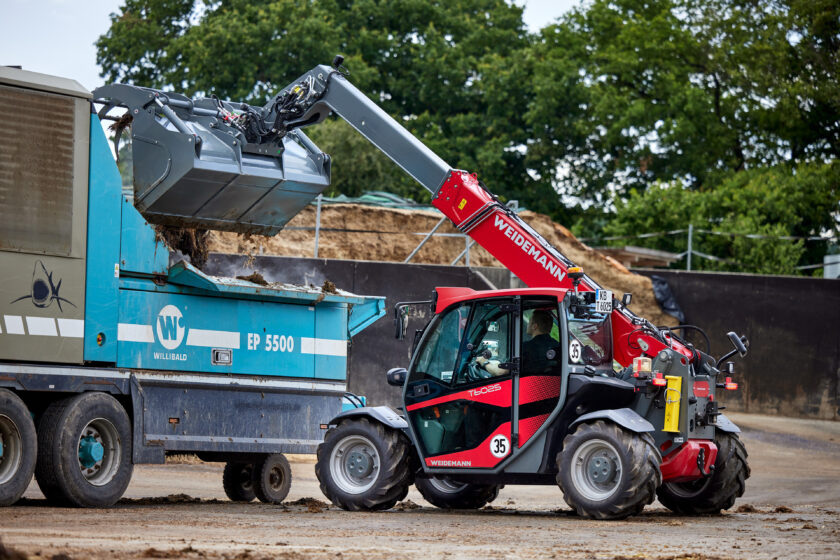
It is no coincidence that all major manufacturers in the sector offer similar machines, capable of raising the arm’s pivot point to nearly six meters while delivering a maximum capacity of 2.5 tons. This capacity is sufficient for handling big bags, buckets for bulk materials, and the densest, largest square and round bales. To simplify stacking tasks, Weidemann has equipped the “T6025” with the “VLS” (Vertical Lift System) as standard.
This system assists the operator during load lifting and lowering operations through the partial, automatic extension of the telescopic arm and its retraction during lowering. This ensures rapid and smooth movement sequences without compromising the machine’s stability, as the load is never subjected to overload conditions. This system, similar to that used on higher-class telehandlers, underscores Weidemann’s aim to promote the “T6025” as a highly versatile machine—a multipurpose vehicle that is compact in size but uncompromising in performance and operational capability.
Engines: 61 or 67 HP
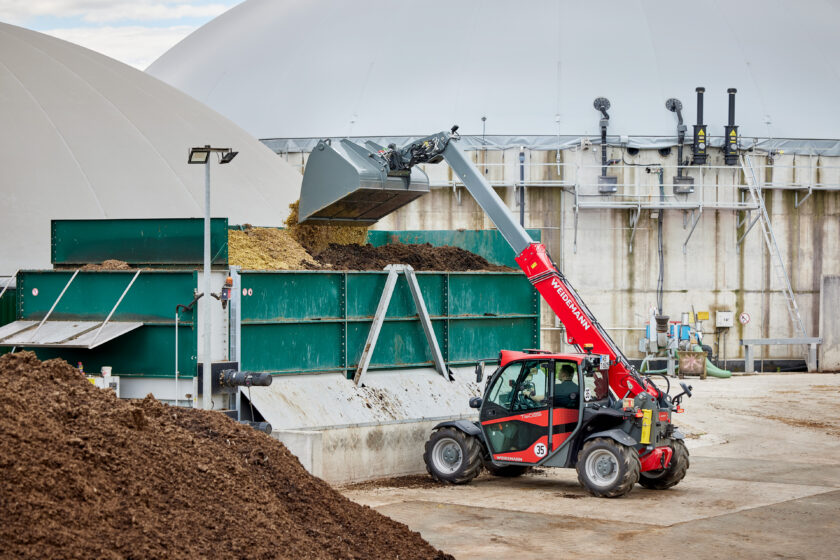
The “T6025” surpasses higher-powered models in versatility due to its height and width, both under two meters, enabling access to older structures. Operational potential is further enhanced by an optional 75-horsepower engine, compared to the standard 61-horsepower unit. The engines, branded Perkins, meet current Stage V environmental regulations through a post-treatment system using DPF and DOC filters with automatic regeneration. These engines pair with electronically controlled “ecDrive” transmissions offering three operating modes. The standard automatic mode optimizes performance by adjusting engine speed to power demands. The “Eco” mode reduces engine speed to minimize fuel consumption and noise, while the “M-Drive” mode allows manual throttle control, ideal for tasks requiring constant speed, such as fertilizer spreading or short-distance material handling. In confined spaces, an integrated steering system with counter-phase wheel movement aids maneuvering. Optional steering modes include crab steering and traditional steering. Regardless of steering mode, the machine features permanent all-wheel drive, enabling maximum propulsion effort on any terrain.
360-Degree Visibility
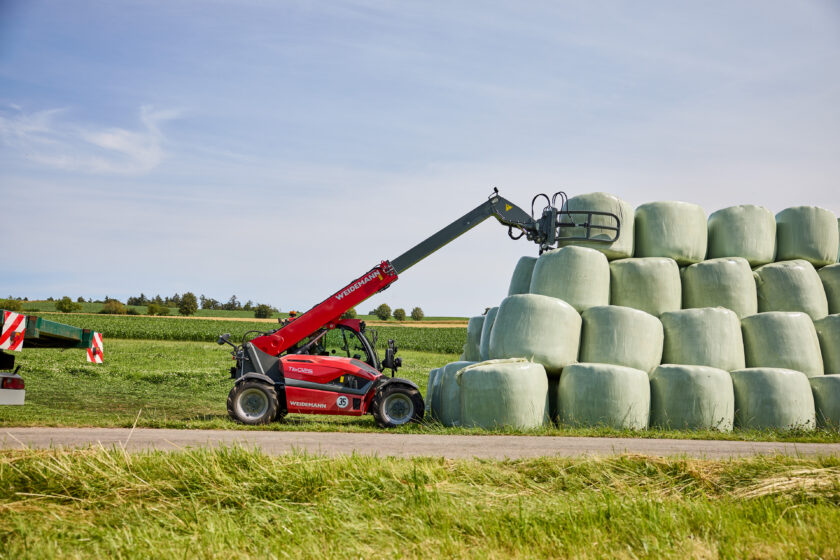
The cabin offers notable comfort levels, sharing structural features with higher-class machines, including nearly 360-degree visibility. This is facilitated by a large, curved windshield extending toward the roof and a standard transparent roof hatch. Also standard are a large right-side window and front, rear, and roof wipers. Together with a raised driving position and a compact engine hood, these features ensure optimal visibility of the work area and surroundings. The interior is more spacious than the external dimensions suggest, with easy access and ergonomically arranged controls. Comfort is further enhanced by a powerful heating and ventilation system, while work efficiency benefits from a multifunction joystick enabling single-handed control of the machine and arm.
New Analysis and Diagnostic System
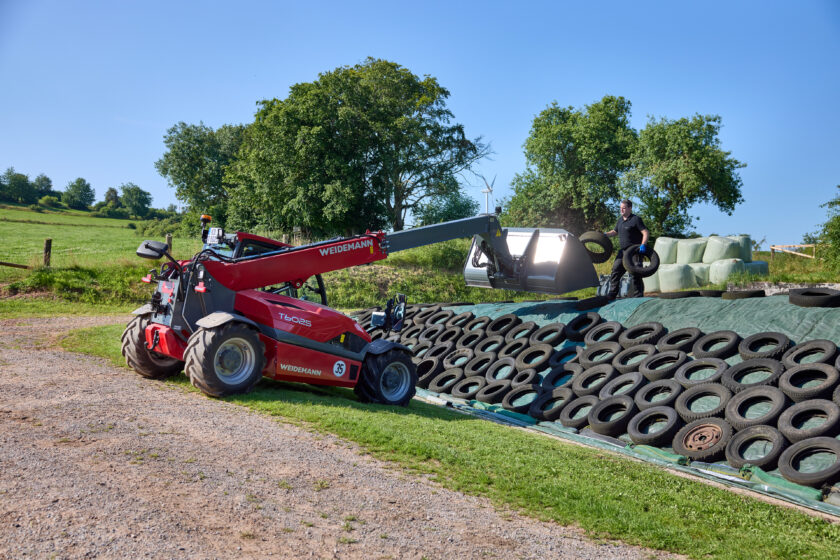
A display within the operator’s view provides essential operational information, supported by the “EquipInspector” diagnostic and analysis system. This monitors driving functions, the telescopic arm, and the third hydraulic circuit. Overall, the machine impresses in terms of performance and ergonomics, with customization options from Weidemann’s extensive range to tailor the vehicle to specific operational needs.
Many Useful Functions
The “T6025” can be equipped with various optional features to simplify and accelerate specific tasks. For example, a load oscillation damper prevents swaying during high-speed transfers, even when transporting loose materials in an open bucket. An automatic return-to-dig function aids repetitive stacking and loading tasks. Additional features include a button for memorizing the tilt cylinder position, a bucket shake function for easier unloading of sticky materials, and a tilt cylinder lock for safe, comfortable handling of heavy loads.
Beyond the First Half-Century
This year, Weidemann celebrates the 50th anniversary of its “Hoftrac” series of loaders, which enabled the company to transition from producing machine components to becoming a self-propelled equipment manufacturer. Founded by brothers Reinhold and Oswald Weidemann, the “Hoftrac” loaders were developed to handle heavy indoor work, particularly in barns, and were designed to be compact, maneuverable, and mechanically simple. Following the launch of the first model, the “Perfekt 1320” in 1974, the series achieved rapid commercial success. This allowed the company to expand production and outsource component manufacturing, focusing on perfecting its loaders. Over time, the product line grew to include wheel loaders, telescopic wheel loaders, and, most recently, telehandlers—the vehicles Weidemann now sees as key to its future growth.
Title: Weidemann T6025: compact only in size
Translation with ChatGPT