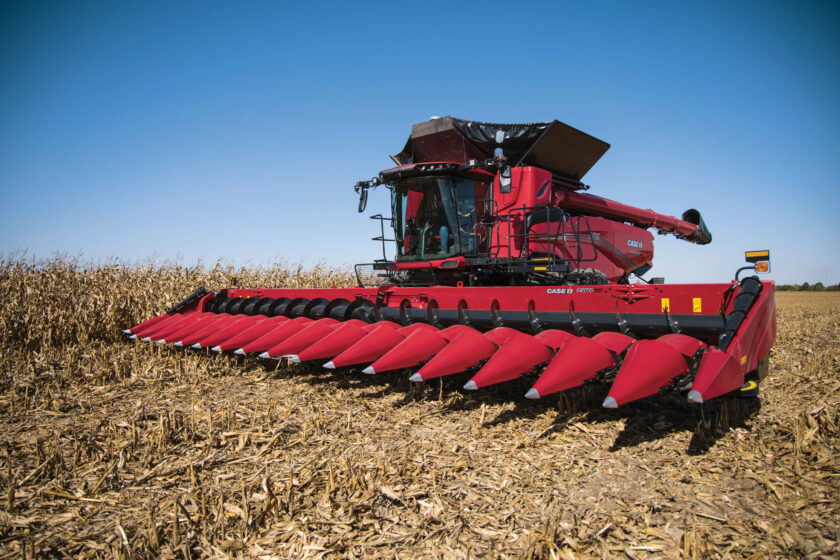
Initially marketed only in North America, the new top-of-the-line axial combine harvester “Af11” by Case Ih aims to redefine industry performance standards not only in terms of power output but also, and above all, in terms of hourly productivity and automation of operational processes.
Based on the latest agricultural censuses in Italy and the United States, the average surface areas of the two primary sectors show incomparable extensions. 188 hectares beyond the Atlantic Ocean, 14 and a half hectares in the Belpaese. An almost abysmal difference that, although known and justified by the different orographic conformations of the two countries, seems to fully justify Case Ih’s choice to present and start exclusively marketing the new top-of-the-range “Af11” combine harvester in North America, aimed at supporting intensive harvesting cycles performed over large areas.
New performance category
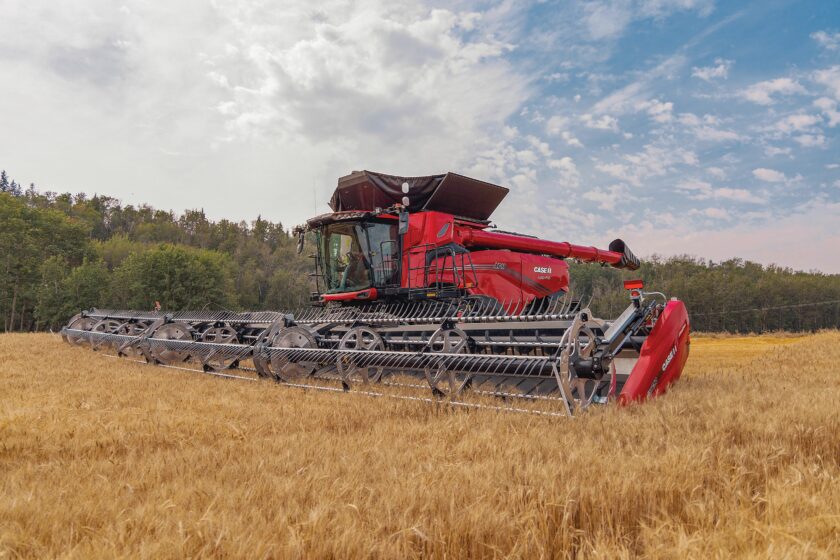
An acronym for “Axial Flow 11”, the acronym condenses the traditional designation with which the American brand identifies its axial-flow combines with the machine’s reference class, which with its 775 horsepower of maximum power exceeds the limit of 680 horsepower that according to the parameters of the Association Equipment of Manufacturers classify class 10 combines, the highest level currently among the official ones. The new “Af11” thus inaugurates a new power class, raising the performance bar not only in terms of power but also in terms of hourly productivity and automation of operational processes, positioning itself as a new industry benchmark thanks to the field-tested capacity by Case Ih technicians to harvest over two thousand quintals of corn in one hour while working at speeds exceeding 11 kilometers per hour.
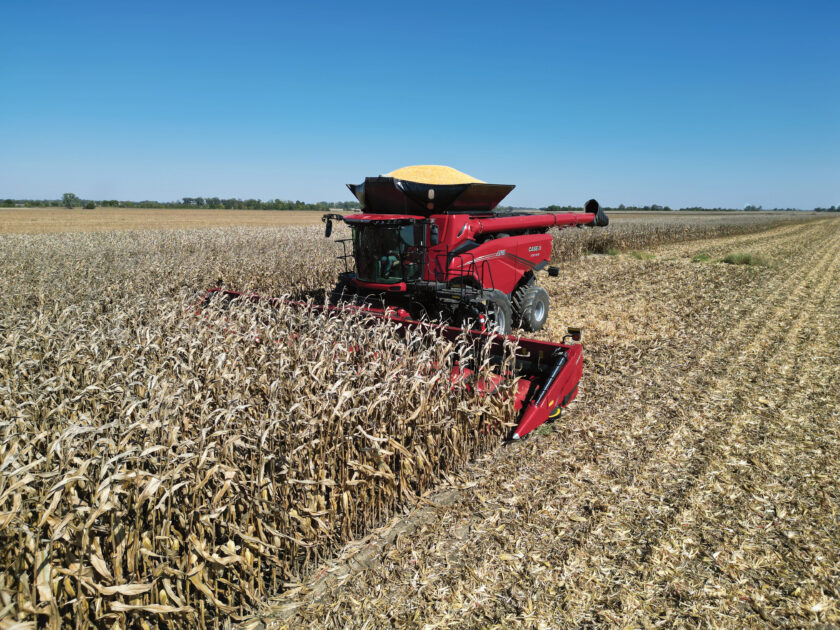
These results are achieved through the innovative “AfXl2” biaxial separation system, instead of the traditional Case Ih single-rotor technology, developed based on a Cnh Industrial design platform that envisages a linear kinematic chain aimed at maximizing operational efficiency by minimizing energy dissipation. For this reason, the engine, a “Cursor 16” six-cylinder engine with 15 liters and 900 cubic centimeters of production by Fpt Industrial, has been mounted longitudinally at an angle equal to that of the rotors, while the latter, elongated compared to the single-rotor equipped on the “Axial Flow” already on the market, are driven by a transmission box located centrally on the machine that also powers the feeder channel and the harvesting heads.
Engine placed longitudinally
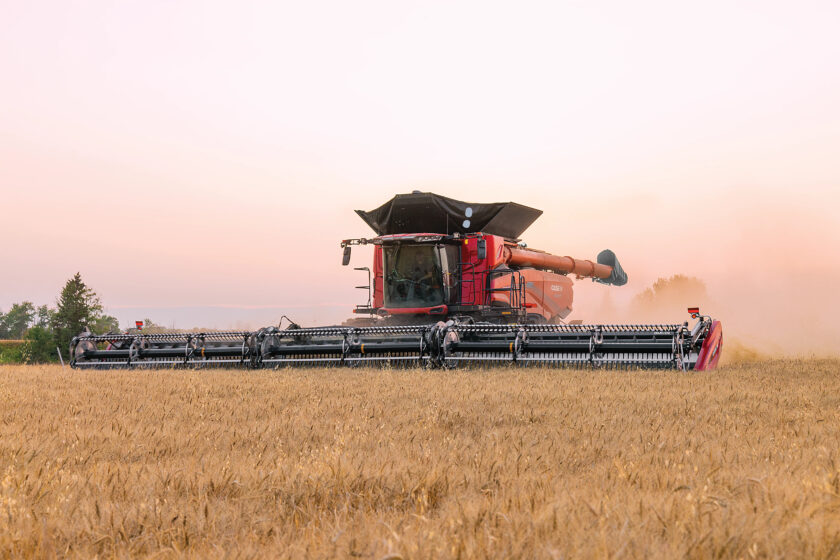
The result is a functional optimization of the working organs that also helps to free the lateral structures of the frame from mechanical encumbrances, thus ensuring more operating space for the separation systems, and better accessibility for maintenance. The increased performance offered by the new “Af11” has also required both an enlargement up to 20,000 liters of the grain tank, which can be emptied at a rate of 210 liters per second, and a revision of the system designed to eliminate any product blockages induced by intensive harvesting activities and operating autonomously through the temporary reversal of the rotor motion.
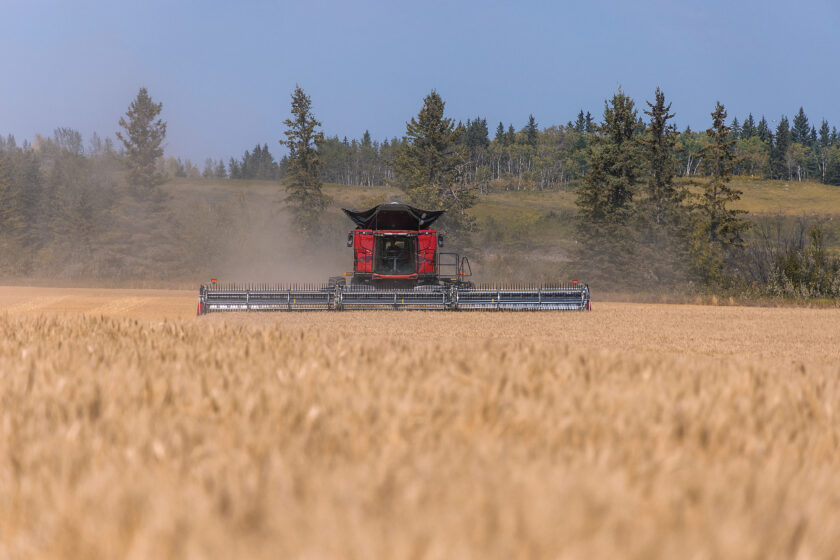
Always with a view to maximizing the efficiency of the separation action, the cleaning surface has also been increased by 45 percent compared to current-generation models, and the pressure control system has been integrated to determine the load of the sieves with special sensors that monitor the longitudinal and transverse distribution of the product on the upper sieve. The automatic “Twin Clean” system operates in fact based on four sieves and an active plate that work the harvested product, keeping it always horizontal, while two transverse augers then convey it to an elevator for the clean grain with a capacity of approximately 352,000 liters per hour, almost 30 percent more than what is proposed by the lower-class “Axial Flow” models.
Always clean horizontally
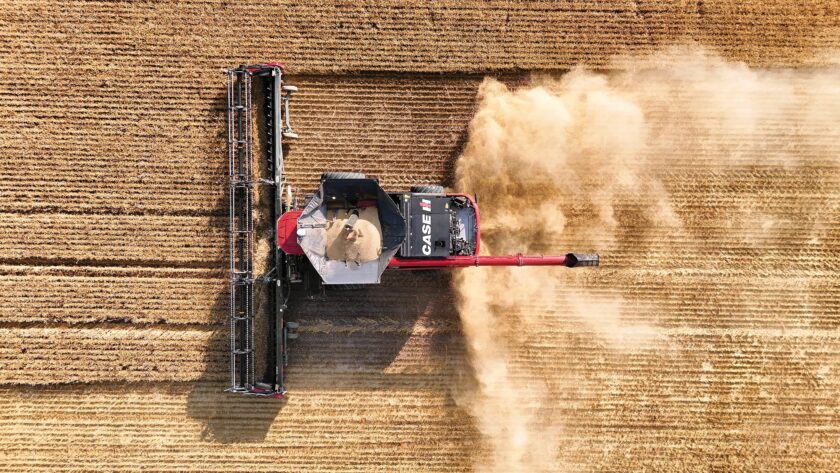
The result is a work efficiency that ranks at the top of the category, playing a strategic role not only in harvesting performance but also in containing product losses and energy absorption, and therefore fuel consumption, which are two important items in the operating costs budget. Finally, to make these costs even more sustainable, both the “Afs Harvest Command” system, which allows the complete automation of the machine’s work, and the “Afs Connect” technology, which enables remote control of field activities and connection with the reference dealer to address any technical needs in real time, contribute.
Title: The lady in red by Case Ih: here is the “Af11” combine harvester
Traslation with ChatGPT