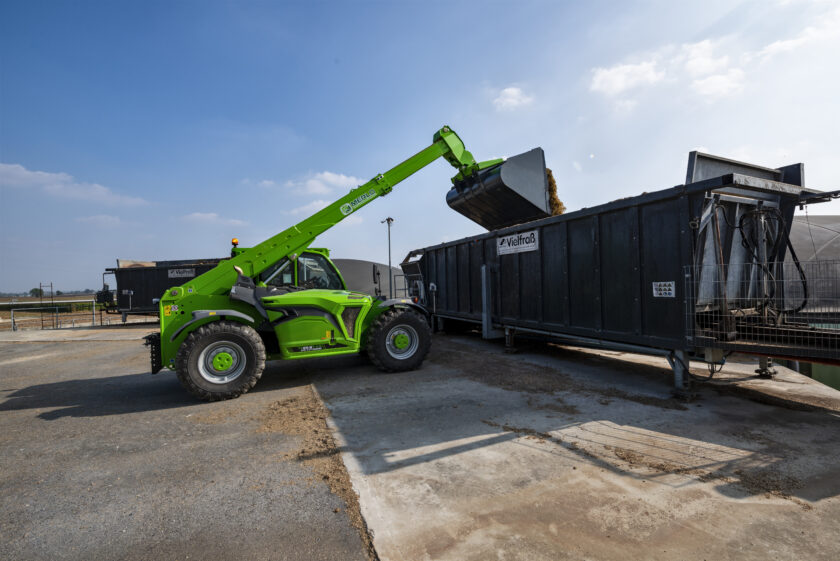
When an agricultural machine has a hydraulic system designed to operate external equipment, it is customary for the system to always maintain this circuit at a minimum working pressure called “standby pressure”, which is necessary to ensure immediate responses to energy demands from operators. This pressure is normally higher than the minimum working pressure and is activated within a few seconds after the machine in question has been started. It is then maintained if the hydraulic system is not used until the machine is turned off.
This results in continuous energy consumption that affects fuel consumption and emissions to a greater extent, the higher the standby pressure, a parameter particularly high in the case of telescopic handlers because most of their functionalities are managed hydraulically. For this reason, and based on the concept that the standby pressure cannot be zeroed, all the most environmentally conscious manufacturers in the sector are working to develop constructive solutions aimed at minimizing the standby pressures of their machines without penalizing their functionality.
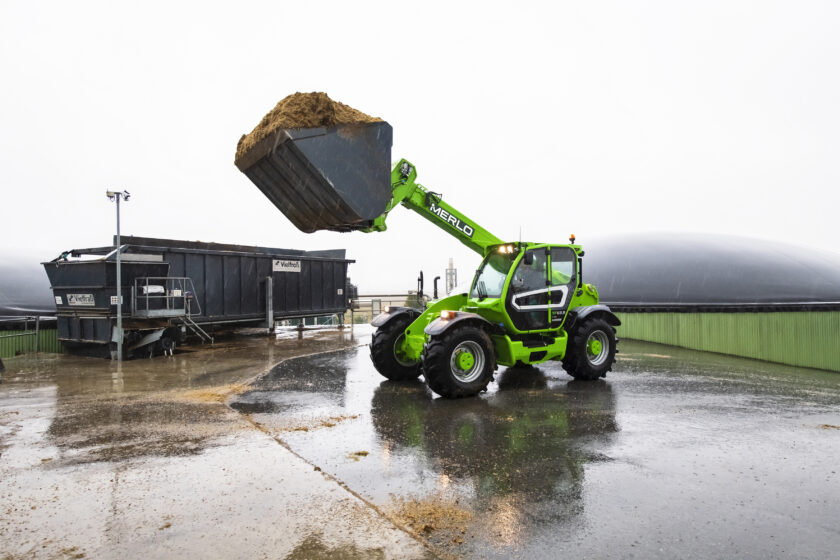
Leading this research is, of course, Merlo, a manufacturer that has been a leader in technological evolution in the sector for decades and has recently confirmed this position by developing a pressure management system aimed at minimizing energy consumption of circuits and therefore hourly working consumption without penalizing, and indeed increasing, their efficiency.
Merlo system “Hi-Flow”
Called “Hi-Flow”, the system of Merlo is based on the presence of a hydraulic pump with a displacement of 72 cubic centimeters operating at a pressure of 250 bar and capable of delivering up to 160 liters of oil per minute. This is complemented by a Merlo-designed distributor labeled “Mh01” incorporating a valve to allow gravity-controlled descent of the arm and a hydraulic suspension system that achieves the floating position of the arm. All of this is integrated into a load-sensing circuit that optimizes the distribution of hydraulic flow to all actuators.
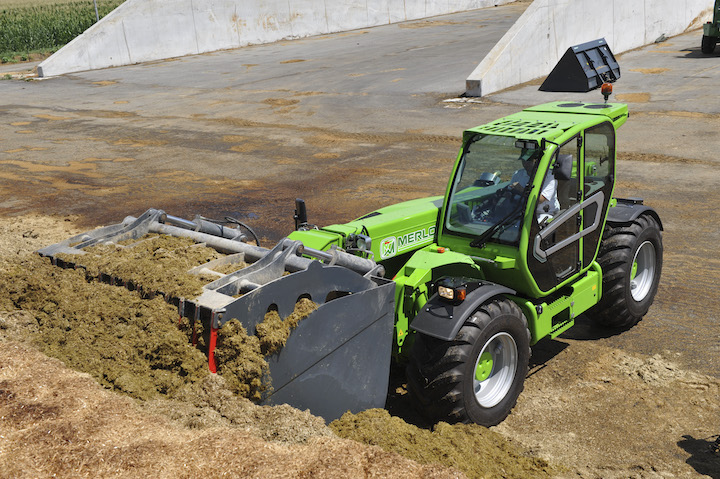
The system, which has allowed the standby pressure to be lowered to just 20 bar, is currently planned for the “Tf50.8”, “Tf45.11”, and “Tf65.9” models but will progressively become available across the entire range to achieve the lowest possible consumption according to the operational demands advanced by operators. This objective is also pursued by the oil passages proposed by the distributor, designed to minimize fluid dynamic friction and the inevitable overheating to which the fluid is subject when working. Furthermore, the system is integrated into the Merlo stability control system, achieving setpoint functions and the aforementioned flotation.
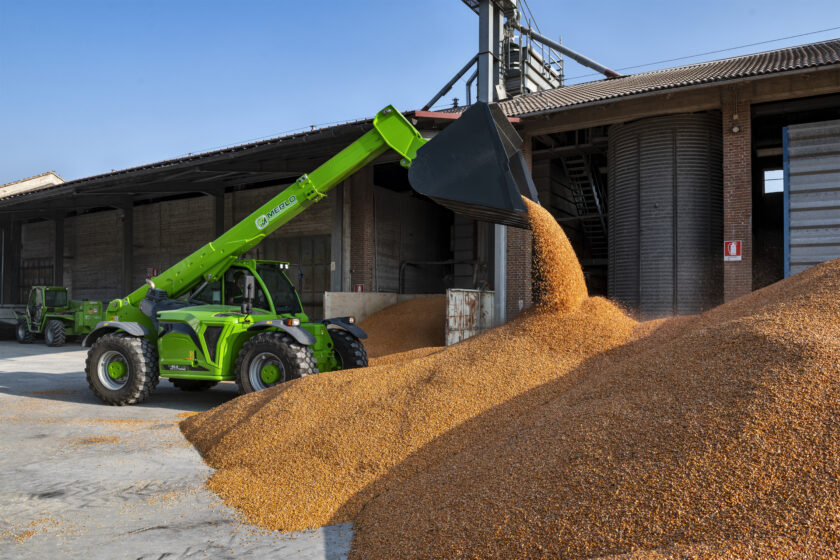
The first allows pre-programming of the arm’s working points so that they can be recalled with a button press, allowing the system to then control the hydraulics to reach them in the shortest possible time. The arm flotation function allows the arm to follow the terrain contours, eliminating blocks that limit the movement of the lifting cylinder and keeping the raft and extraction rotation systems active. This functionality facilitates work with shovels, snow blades, and, more generally, with all tools that require constant contact with the ground. This is done without compromising the execution of other arm or machine movements such as extractions or retractions, raft inclinations, management of auxiliary hydraulic outlets, and, if provided, tilting and chassis translation systems.”
Title: Merlo system “Hi-Flow”
Taslation with ChatGPT