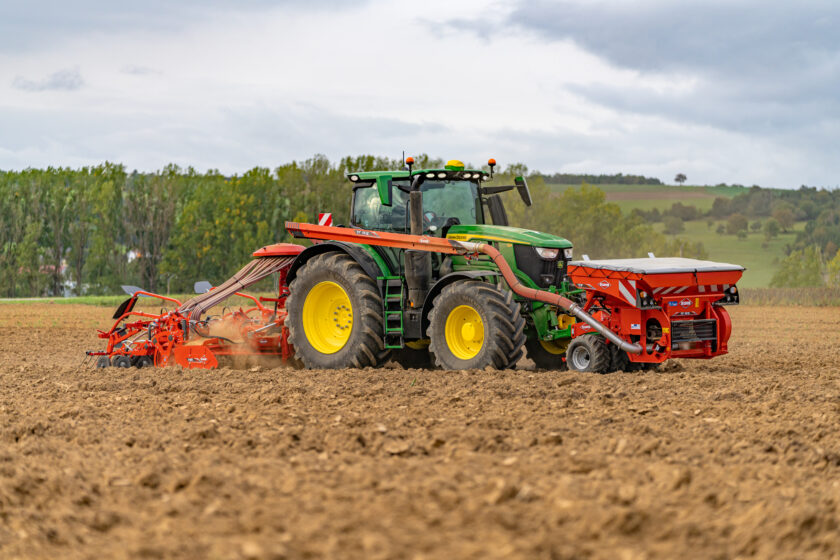
The combination of multiple implements to carry out different but sequential or related tasks in a single pass has become standard practice in the agromechanical field, as it allows for significant time and fuel savings. An example of this is the combination of seeding equipment with tools for soil refinement, a practice that has been common for years and has proven advantageous in terms of reducing both working time, which is halved, and fuel consumption, which significantly decreases, becoming lower than it would be if the two operations were performed separately.
Disc harrowing is favoured
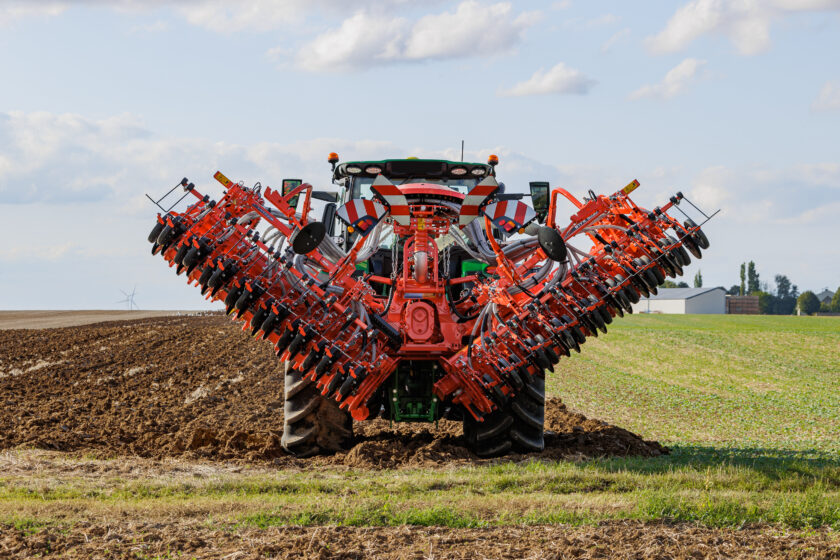
Experience gained over time by both manufacturers and field operators has also led to a preference for disc harrows, generating two different schools of thought. On one hand, some prefer implements with passively pulled discs because they allow for maximum operating speeds.
On the other hand, others favor power harrows driven by the tractor’s power take-off, which provide better soil refinement and the ability to work at greater depths, up to 25 centimeters.
Regardless of the operating mode of the discs, a common feature of both types of activation is the ability to manage crop residues thanks to the rotational action of the discs, which shred the residues and mix them with the soil matrix, improving its structure and thus its ability to absorb and retain water—a quality that is expected to become increasingly valuable in the future.
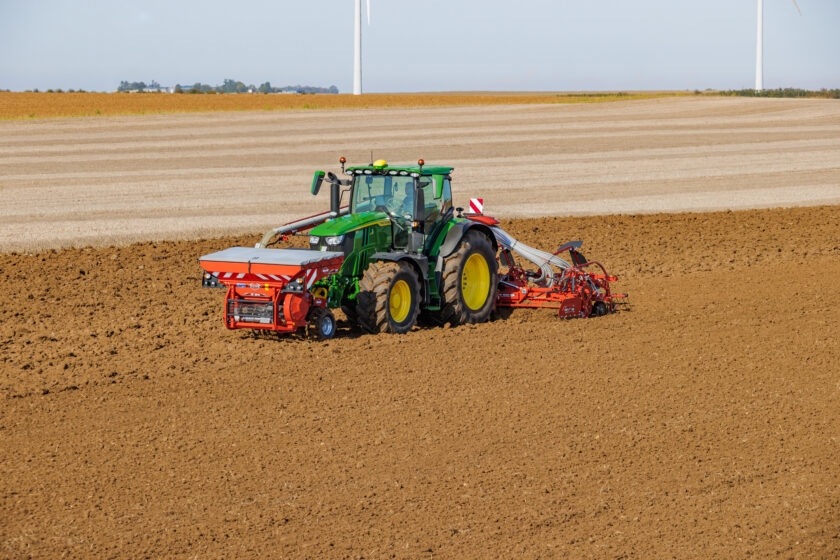
All indications suggest that the demand for combined seeders is likely to grow, which is why it is no surprise that Kuhn has introduced several of its machines as options for farmers in the market. It should be noted that Kuhn was already present in this sector with a six-meter-wide combined implement, based on the combination of a “Btfr 6030” pneumatic folding seeder and an “Hr 6040 Rcs” power harrow. However, this setup is aimed at more structured farms due to the need for very high-powered tractors, around 460 horsepower.
Kuhn has now enriched its portfolio of combined implements with less demanding solutions by combining its “Btfr” series pneumatic folding seeders with the “Hr” series power harrows. This has resulted in three solutions based on the combinations “Btfr 4030+Hr 4030 Rcs,” “Btfr 4530+Hr 4530 Rcs,” and “Btfr 5030+Hr 5030 Rcs,” which deserve special attention as they are capable of meeting the needs of farms and service providers with tractors of 300 or 350 horsepower, depending on whether the working width is four meters, four and a half meters, or five meters. Common to all these solutions are the “Seedflex 1000” seeding units, characterized by different row numbers depending on the model. For the “Btfr 4030,” the number of rows ranges from 26 to 32, rising to 30-36 in the “Btfr 4530” model and ending with 32-40 in the “Btfr 5030” model.
Center of gravity closest to the tractor
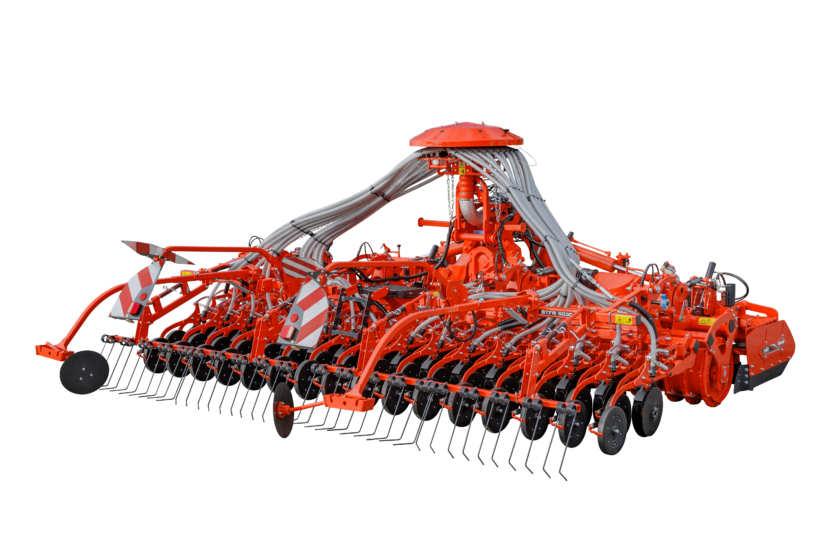
To ensure maximum soil contact, the “Seedflex 1000” units are installed on the same frame that supports the power harrow roller, a placement that also has the advantage of moving the center of gravity closer to the tractor, stabilizing the implement and reducing potential imbalances when the terrain is not perfectly level. Available with a row spacing of 12.5 centimeters or 15 centimeters, the seeding elements feature staggered double discs measuring 41 millimeters, which provide precise furrow opening, an objective further aided by the beveled disc profile that improves penetration and cutting on all types of soil. To ensure long-term functional reliability, the units are equipped with reinforced bearings protected by the disc itself, as well as solutions designed to safeguard the equipment in the event of impact. On the rear units, there is a safety device designed to fold under pressure or in case of extreme movements, thus avoiding the need to replace the entire unit in case of breakage caused by a large obstacle. Should it become necessary to replace or service the discs, they can be quickly and easily removed by acting on just a few bolts.
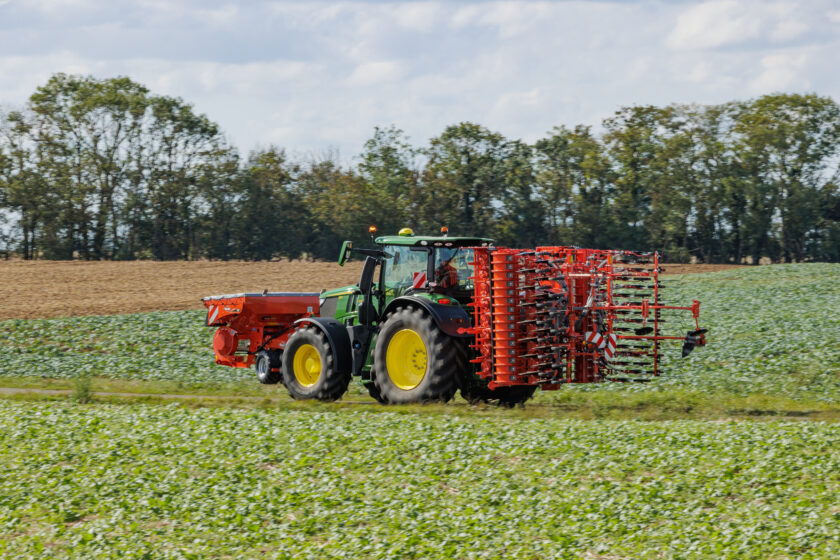
The precision of seeding depth is maintained by the fact that the double discs are mounted on a solid parallelogram frame, which is hydraulically operated, while specific compaction wheels adequately close the furrow after seed deposition. The distribution of the seeds is managed by “Vistaflow” valves, which allow for universal tramline creation directly from the cab. The precision of these valves is ensured by an intelligent monitoring and detection system that automatically sends a warning signal to the tractor terminal in case of blockage in one or more rows. This function is carried out by optical flow sensors placed on each valve, capable of detecting partial blockages, such as those caused by straw fragments in the distribution tube.
Finally, in terms of field autonomy, the three new models rely on the “Tf 1512” front-mounted hopper, managed via ISOBUS protocols, with a base capacity of 1,500 liters, extendable to 2,000 liters with an extension. The front position of the hopper also achieves an optimal balance between front and rear masses, further stabilizing the implement and enhancing seeding precision and uniformity.