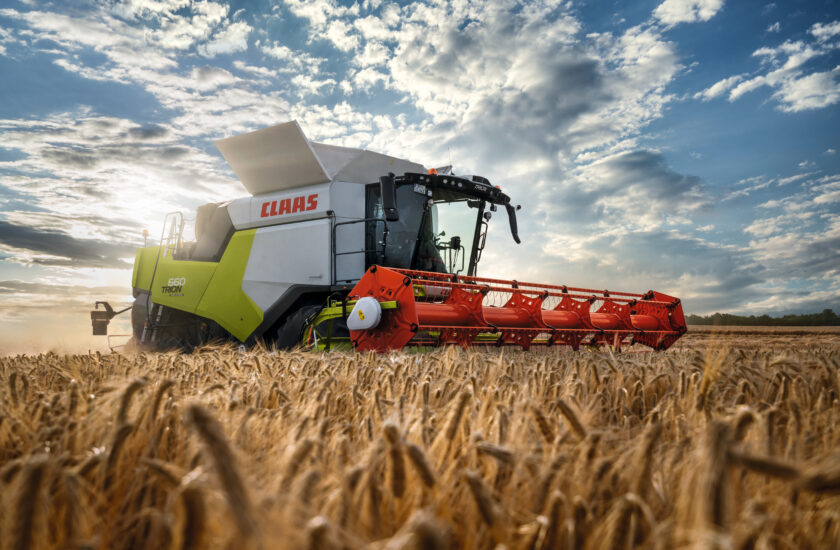
Held in Dubai, United Arab Emirates, from November 30th to December 12th, the 28th edition of the United Nations Conference on Climate Change, abbreviated as “Cop 28,” has repositioned agriculture at the center of the global economic-environmental scenario. The annual meeting of the countries that participated in the event has indeed changed the traditional paradigms of discussion for the first time, omitting both the usual generic and predictable speeches regarding the need to protect the environment and those fanciful proposals for epochal changes that in Europe materialized in the utopian program “Green Deal.” The discussions were therefore based on a healthy realism, highlighting the importance of the primary sector in terms of food sustainability and climate resilience.
According to the United Nations report, in 2022 there were indeed 735 million malnourished people globally due to the effects of climate change, which also led to a productive contraction in agriculture with a consequent rise in prices that worsened living conditions in developing and emerging countries. In this context, the only feasible path to avoid facing what has been defined as “the worst food crisis in history” in the near future is to push towards a sustainable increase in production in order to ensure access to essential food items for every person.
Claas “Trion” range, strategic yields per hectare
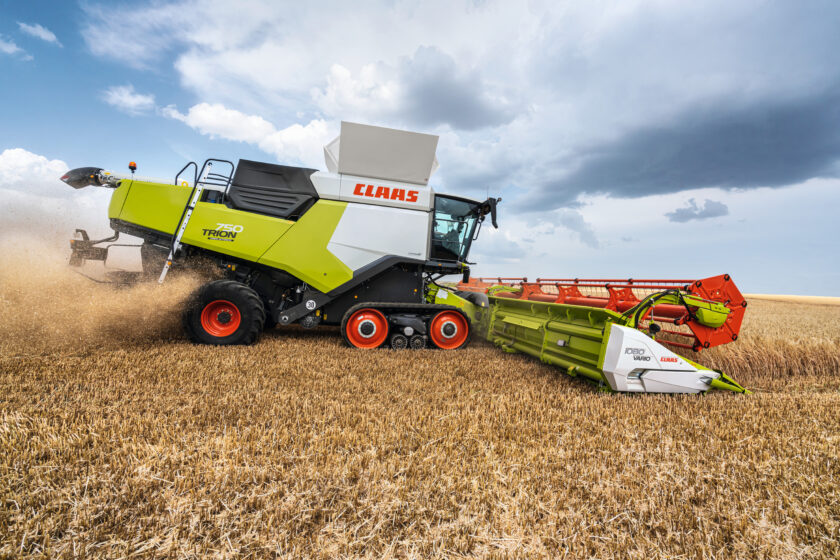
However, this challenge can only be overcome through an increase in average yields per hectare achieved by focusing on mechanization, i.e., through machines capable of ensuring higher productivity for all operators in the sector, not only for large agricultural entities and third-party organizations but also for medium-sized companies that represent the connective tissue of the agricultural economy in many Western countries. It is no coincidence that precisely medium to large-sized companies are the target audience towards which Claas has oriented its range of “Trion” combine harvesters, medium-class machines that, through three different series named “700,” “600,” and “500,” provide even less industrialized companies with all the technologies and operational solutions currently made available by the German company on its flagship “Lexion” models. Firstly, the threshing system “Aps,” shared by the entire “Trion” range and structured based on three groups—an accelerator, a beater, and a thrower—allowing the separation of up to 20 percent more grain compared to a traditional primary system.
Overloads? No problem
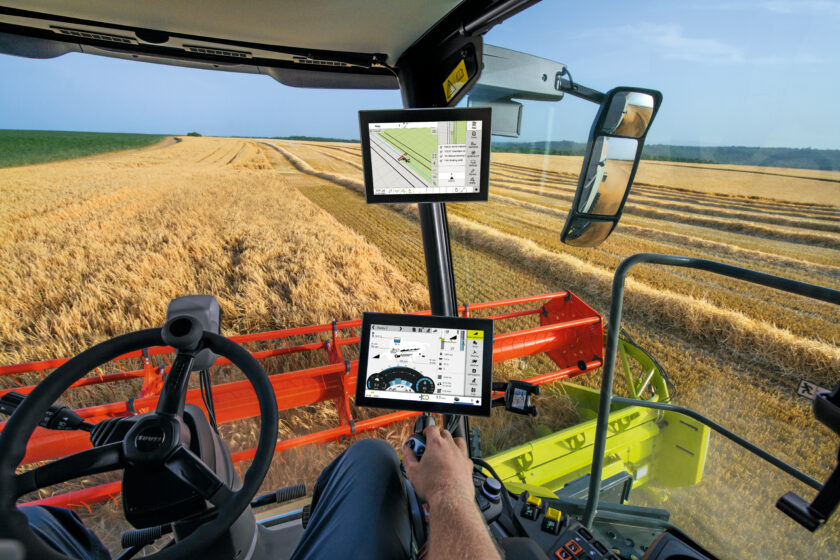
This goal is also pursued by the presence of a hydraulic adjustment system for the counter-beater and an overload safety device, with the former allowing the adjustment of the counter-beater’s setting directly from the cabin based on any changes in harvesting conditions, while the latter protects working parts in case of entry of foreign bodies through the hydraulic opening of the grids during pressure peaks. All solutions are aimed at facilitating the separation process, which on the top-of-the-range “Trion 700” series machines is based on Claas’ proven hybrid system, with a single rotor on the “720” and “730” models and a double rotor on the “750” model, capable of ensuring an increase in productivity of up to twenty percent with the same energy absorption, ensuring gentle treatment of the grain regardless of the type of product being processed. This is also thanks to the fact that the accelerator, beater, and thrower can be driven by a central variator that synchronizes their rotations, and the adjustment possibilities offered by the counter-beating elements.
Claas “Trion” range, five or six straw walkers
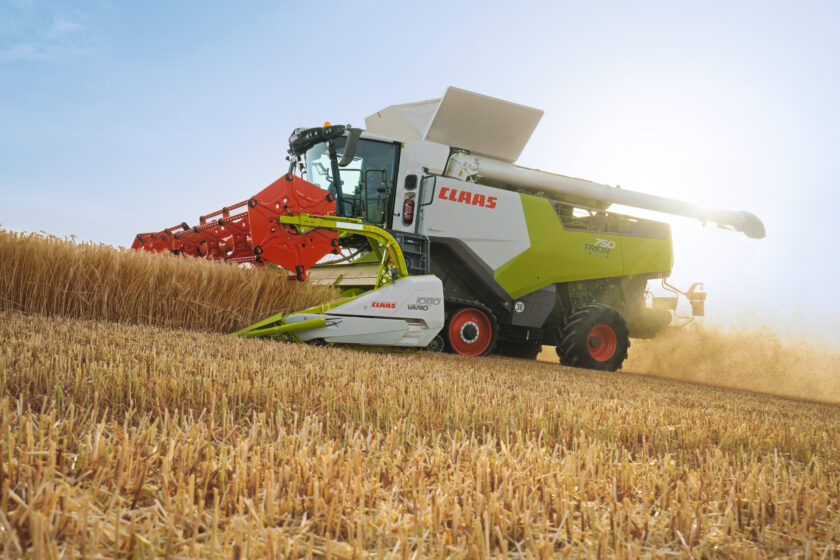
The “Trion 500” and “Trion 600” series, respectively, operate based on five and six straw walkers with four drop steps, for total separation surfaces of over six square meters in the case of the “Trion 500” and almost seven and a half square meters on the “Trion 600.” In both configurations, the separation process is further emphasized by the presence of the “Mss” system, “Multifinger Separation System,” a cylinder with guided fingers designed for intensive airing of the product to ensure optimal separation of the grain even in difficult harvesting conditions.
Optimal cleaning always
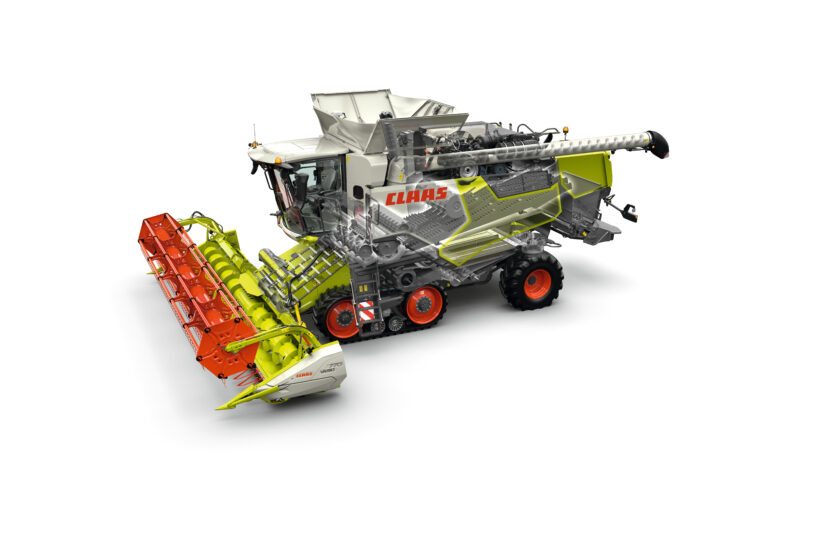
Common to the entire “Trion” range is the presence of the “Jet Stream” cleaning system, operated by a six- or eight-stage turbine fan, depending on the model, and a double ventilated step, a solution that ensures a high-pressure air flow on the sieves that can be adjusted from the cabin and can integrate the “Auto Slope” function to automatically reduce or intensify air flow when working uphill or downhill, also adapting to the harvesting speed. In such application areas, the “Trion” machines can also benefit from the “3D” functions, on the straw walker models, and “4D” on the hybrid versions, which ensure perfect cleaning of the grain when the machines operate on sloping terrain.
Engines from the Stars and Stripes
Configured in this way, the “Trion” combine harvesters aim to ensure maximum operational efficiency regardless of harvesting conditions, also supported by the dynamic support provided by Cummins engines from the “B6.7” and “L9” series, respectively with six liters and 700 and eight liters and 900 cubic centimeters. Delivering a range of maximum power between the 258 horsepower of the entry-level “Trion 520” model and the 435 horsepower of the top-of-the-range “Trion 750” version, the units are characterized by the presence of high-pressure common rail fuel systems and four-valve distributions per cylinder, which together contribute to achieving maximum torque curves that peak at 1,900 rpm during operation and 1,650 rpm during road transfers, values that effectively favor the minimization of energy absorption and, consequently, consumption.
Claas “Trion” range, up to ten percent
This latter objective is further supported by the “Dynamic Power” system, which continuously optimizes the ratio between delivered performance and power demand, adjusting delivery curves accordingly to ensure that the machines can always operate with maximum efficiency and minimal consumption, up to ten percent less than those proposed by a similar engine without this mapping. Stage V certified through scr systems operating jointly with doc catalysts and dpf particulate filters, without the need for egr systems, the engines are then interfaced with a transmission called the “Claas Power System,” created by combining a hydrostatic group with a manual gearbox with two selectable button-controlled ratios, which in turn actuates the “4Trac” traction system, a group operating on the front wheels through reinforced reducers and on the rear wheels through dedicated hydraulic motors, integrated with a slip control system that facilitates travel on softer ground.
“User-friendly Automations”
With a view to maximizing harvesting efficiency, the “Trion” combine harvesters also allow delegating the management of separation groups to the “Cemos” system, an onboard software that integrates all the functionalities aimed at optimizing the machine’s settings through two different operating versions. The first, called “Cemos Dialog,” enables progressively optimizing adjustments based on a dialogue between the machine and its operator, while the second, “Cemos Automatic,” automatically and intelligently adjusts the machine settings to different harvesting conditions. In this perspective, the “Auto Header” and “Cruise Pilot” functions manage, respectively, the cutting platform “Vario” and the forward speed, while the systems “Auto Threshing,” “Auto Separation,” “Auto Cleaning,” “Auto Crop Flow,” and “Auto Slope” are responsible for adjusting, respectively, the threshing system, residual grain separation, cleaning system, product flow, and fan air volume.
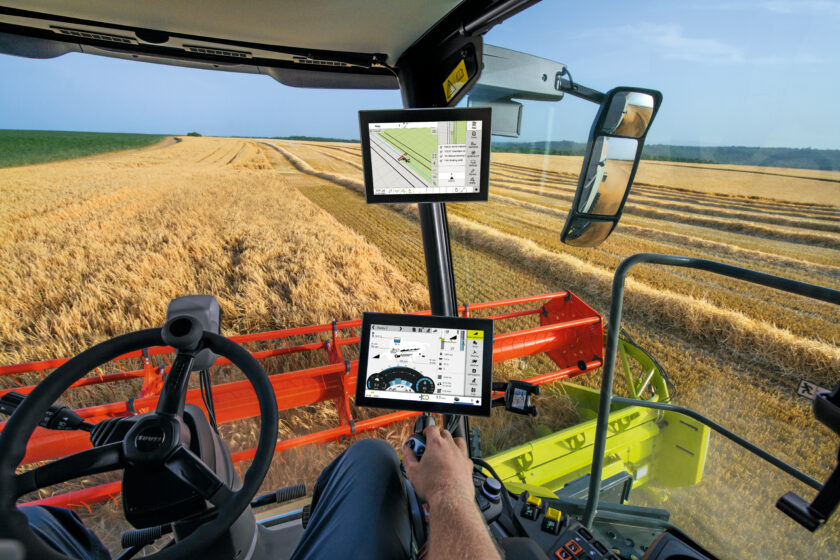
The “4D” and “Auto Chopping” functions then control the rotor grid blinders based on slope and manage residues and straw chopping, including the width and direction of distribution of the shredded product from the “Standard Cut” system with 52 knives on the “Trion 500” and “Trion 700” models, or with 64 knives on the “Trion 600” versions, replaceable optionally with the “Special Cut” group with 72 or 88 knives. Thanks to this, operators can delegate the management of functional and operational systems to onboard systems to focus exclusively on driving the vehicle, while acknowledging that this activity is also automatable through three different automatic steering solutions. Traditional harvesting activities are addressed by the “Laser Pilot” system and the “Field Scanner” function, allowing the combine harvester to work without overlap passes through a specific laser system. At the top of the Claas offering is the satellite guidance system “Gps Pilot,” which allows the machine to advance with margins of error on the order of two centimeters, transmitting its functional parameters in real-time through the “Cemis 1200” terminal and the “Telematics” telemetry system to the company’s technical offices.
Claas “Trion” range, extreme Performance
Offered in almost all models, both in hillside configuration “Montana” and tracked version “Terra Trac,” the “Trion” range also debuted last summer with a version dedicated to harvesting activities conducted on steep slopes. “Trion 540 Montana 4,” the name of the machine, operates based on the same conventional system with five straw walkers proposed by all models belonging to the “Trion 500” series, while at the propulsion level, it shares the same engine as the plain version “540,” effectively the six-cylinder Cummins “L9” series engine of eight liters and 900 cubic centimeters, with a maximum rating of 354 horsepower. The unit is also integrated into a powertrain based on a new two-speed hydrostatic transmission, field, and road, and an original Claas rear propulsion system that comes into action only when necessary, being of the electro-hydraulic type.
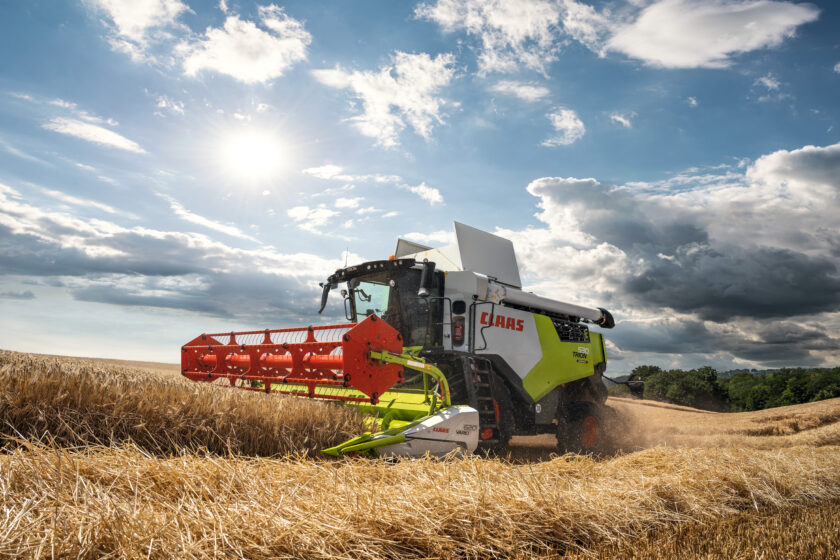
It includes a central hydraulic motor that drives the half-shafts of the rear wheels and, thanks to specific sensors and dedicated electrovalves, can be electronically controlled both in terms of intervention and wheel slip control. The system also benefits from more structured rear tires and, thanks to the pendulum design of the axle, allows for tighter turning radii compared to the past, thus favoring higher maneuverability, a trait that is particularly evident when the combine harvester is called upon to operate on steep slopes. The electronic management of the leveling system not only allows for tackling lateral inclinations of 38 percent, climbs of 32 percent, and descents of 11 percent even under maximum load conditions but also enables safe maneuvering, achieved by refining and improving all components of the three basic parts of the leveling system: the frame, the front axle, and the rear axle. The frame is made of high-strength steels and can withstand loads of up to 25 tons, the front and rear leveling cylinders boast reinforced supports and stems but operate at low operating pressures to reduce stresses on the hydraulic system, and the stabilizer bar is in two parts to improve reliability.
Title: Claas “Trion” range, a combine harvester with solid performance
Traslation with ChatGPT