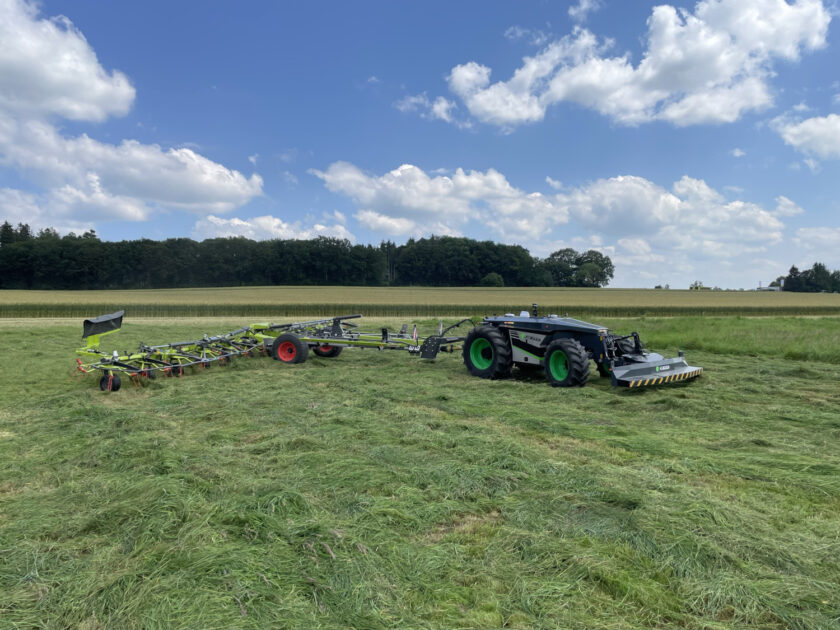
For many farms, forage harvesting is one of the most demanding phases, especially for the first cuts. Before and during mowing, fields must be searched or scanned for wild animals, with operations like mowing, raking, windrowing, and uprooting often occurring simultaneously. In the future, autonomous tractors or AgBots could lighten the workload for many farmers and contractors. Tall-growing crops present a particular challenge, as does the continuous monitoring and assessment of work quality. Together with partners like AgXeed and Thermal Drones, Claas is researching and testing various applications to further advance standardization.
A Matter of Interface: Highly Automated Mowing
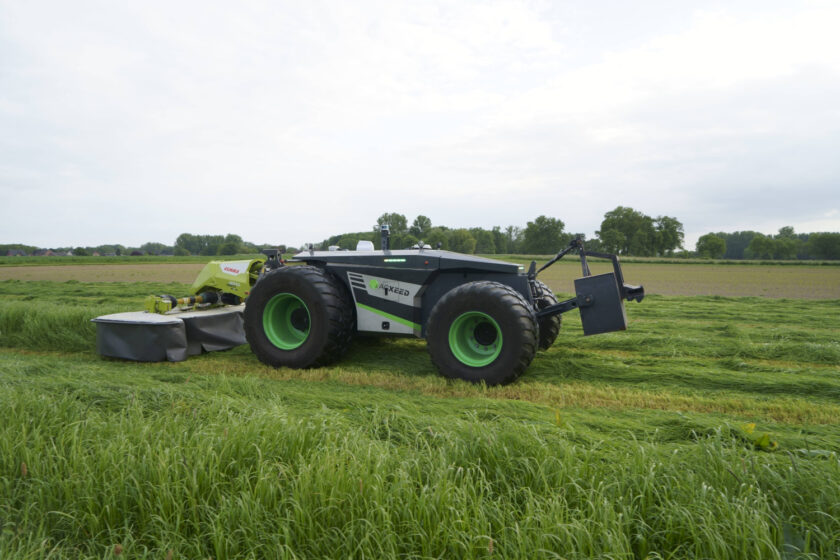
Drones with thermal cameras are now a widespread, safe, and effective means of detecting breeding nests and wild animals, especially roe deer fawns, just before mowing or whole crop silage. The search is generally conducted using a real-time image and paused when a heat source is detected to allow operators to remove the animal and place it in a safe location or mark its position or a nest. Claas, Thermal Drones, and AgXeed have already combined their expertise and developed a common interface for drones in the event of automated mowing. Heat source data obtained during the drone flight is initially stored, then processed with artificial intelligence software and transferred along with GPS position data to the process planning tool. This incorporates the data into route planning, allowing the mower to maintain a predefined and adjustable safe distance around the fawn or nest site. This deviation is particularly useful in fields where protected birds breed, as these nests cannot be removed. Farmers and contractors can track the machine’s movements live on their smartphone, tablet, or PC via the AgXeed platform. In this way, the use of autonomous mower combinations can meet the needs of sustainable and wildlife-friendly pasture management, as well as high yields. Additionally, farmers can document the measures taken before mowing to comply with the obligation to provide supporting documentation.
In the future, this technology will be applicable not only to autonomous field robots but also to autonomous driverless tractors and highly automated guided tractors and harvesting machines that follow pre-set paths. The application is expected to become a viable solution for customers in the coming years. Protections ensure that POI data on wildlife and breeding nest locations are recorded only within known and previously established field boundaries. Field boundaries can be easily transferred from the respective farm’s management system. However, if this data is not available, the drone pilot can mark the field boundaries on the screen.
The Next Step: Monitoring and Controlling Large Working Widths
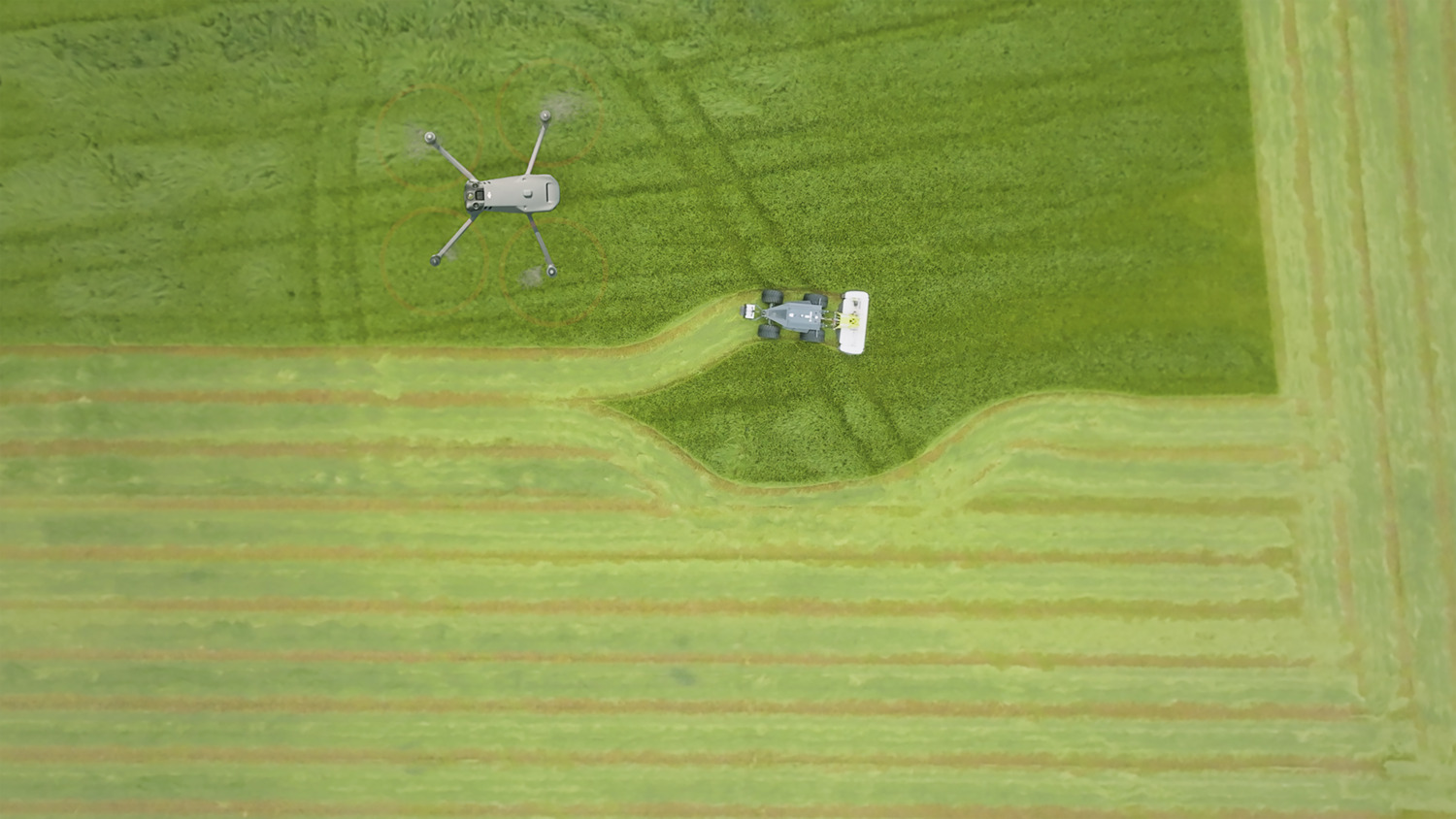
During Editorial Week 2024, Claas and AgXeed demonstrated an AgBot 2.055 W4 with a high-performance VOLTO 1300 T tedder as another possible application.
Standardization is a Team Effort
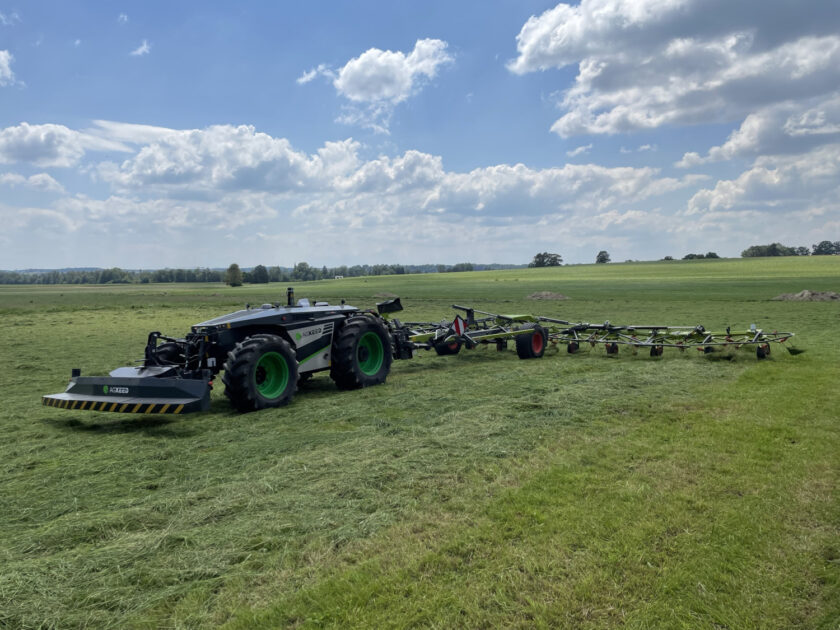
Claas collaborates with associations and partners on further developing interfaces to increase automation of tractor combinations, AgBots, implements, and drones. The results achieved form the basis for the next step towards fully automated and driverless machine combinations. The 3A – ADVANCED AUTOMATION & AUTONOMY consortium has already initiated this effort with the AEF (Agricultural Industry Electronics Foundation) and plans to move forward and involve other agricultural machinery manufacturers.