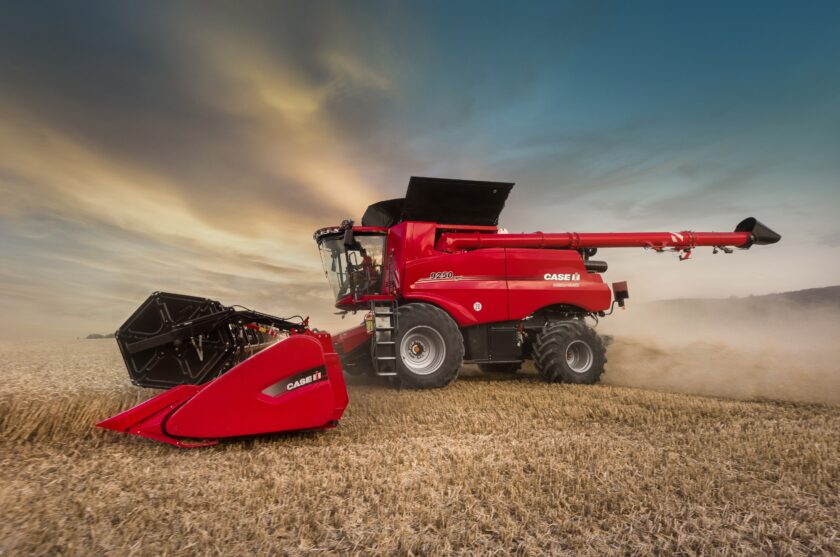
Launched in 1977, Case IH’s “Axial Flow” combine harvester series quickly established themselves in the market as machines capable of operating on a variety of crops at speeds impossible for direct competitors, thus setting higher productivity standards. In addition to this advantage, they also exhibited a strong respect for grain and straw, which more recently extended to soil conservation through the option of replacing front wheels with hydraulic suspended track systems, optionally coupled with a hydraulic propulsion system acting on the rear wheels. Equipped with these features, the machines not only float on the ground, minimizing compaction by up to 43 percent compared to traditional tires, but also proceed without causing the classic and unwanted plowing effect typical of tires on softer soils.
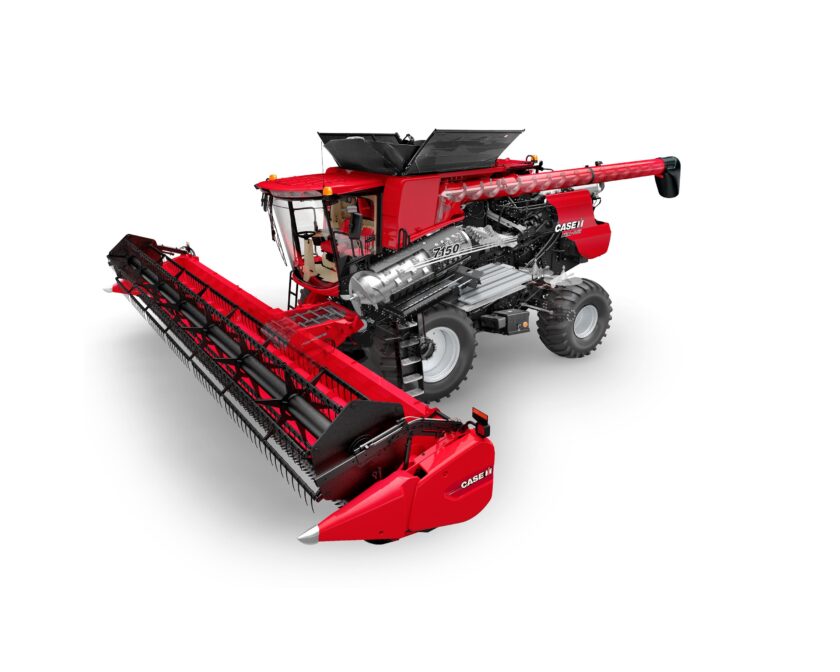
Thus, maximum efficiency is maintained, a statement valid not only in terms of harvesting and separating, but also in managerial terms if operators harness the full potential of the Case IH digital platform “AFS” (Advanced Farming System), which integrates a complete range of computer solutions aimed at facilitating work in all its phases.
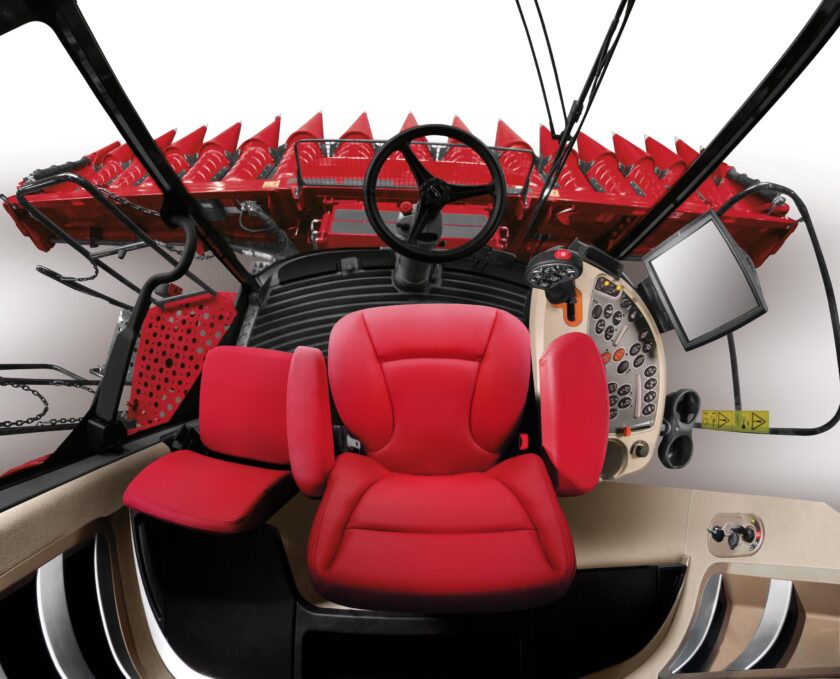
Autonomous guidance is enabled through functions such as “AccuSync” and “AccuGuide” when operating in the field, with the ability to automate even the end-of-row turns. Additionally, presettings of working tools and performance parameters based on the type of crop the machine is dealing with are available, along with the “AFS Connect” functionality that keeps the site constantly connected with company management and dealerships to address any technical or administrative needs in real-time. “AFS Harvest Command” effectively allows for complete automation of the combine, freeing operators to focus solely on overseeing the work. They can intervene on the onboard console or the “AFS Pro 700” touchscreen monitor to adjust the “AFS Harvest Command” automation system settings when necessary to correct programming based on surrounding conditions. In practice, the “AFS Harvest Command” platform requires only two manual interventions from the operator: adjusting the distance of the counter-beater from the rotor and activating the discharge auger, while autonomously controlling all machine settings, from ground speed adjusted according to crop load, to fan speeds, also adjusted based on terrain inclines, and including control of sieve openings and rotor cage fins.
Five models from 400 to 634 horsepower
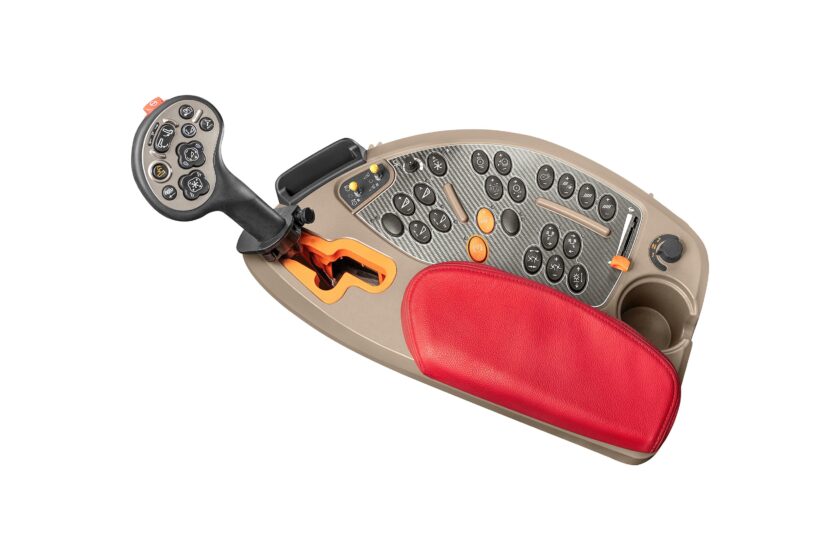
The Case IH “Axial Flow” combine harvesters are available in five models, all customizable in every component based on the needs of each individual farm. Consider, for example, that there are two cabin configurations, and setups are characterized by the presence of a threshing rotor specifically designed for European crops. The machines are divided into two series, labeled “160” and “250,” and are all powered by FPT Industrial “Cursor” series engines paired with hydrostatic transmissions with two or three speeds depending on the model. Tank capacities vary from a minimum of 10,500 liters to a maximum of 14,400 liters, and discharge systems operate between 113 and 159 liters per minute, with spouts controllable at distances of almost nine meters from the machine thanks to the presence of adjustable augers in length.
The Ten Advantages of “Axial Flow”
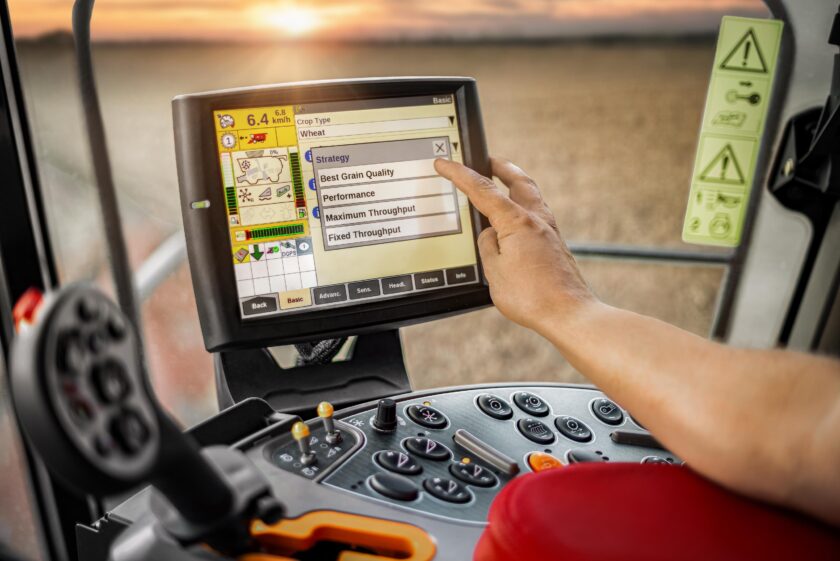
Combines:
Construction quality and reliability, evident in the meticulous attention to detail in every component.
High level of automation provided by the “AFS Harvest Command” system, coupled with its easy and intuitive programming capabilities.
Constant connectivity with company management and dealerships for real-time efficiency monitoring and intervention when necessary, such as when inexperienced personnel are operating the machine, and for implementing a predictive maintenance system.
High-quality final products, with minimal grain loss and breakage, and the option to cut or deposit straw, with adjustable length in the latter case.
Mechanical simplicity and ease of maintenance.
Digital and structural solutions aimed at reducing diesel consumption, including minimizing the use of belt transmissions in favor of direct mechanical connections.
Comfort and spaciousness provided by the cabins, available in two trim levels, one of which, the “Luxury” package, features leather upholstery and a semi-active pneumatic suspension driver’s seat, ventilated and heated, along with a removable refrigerator and electric mirrors.
Field stability ensured by the option to equip machines with rear-wheel drive axles and suspended tracks, resulting in high working speeds.
Efficiency of FPT Industrial engines compliant with Stage V emissions standards, without EGR, thus delivering high performance with minimal fuel consumption.
Efficiency of after-sales service, guaranteeing prompt field interventions and the availability of spare parts within 24 hours if needed.
Traslation with ChatGPT