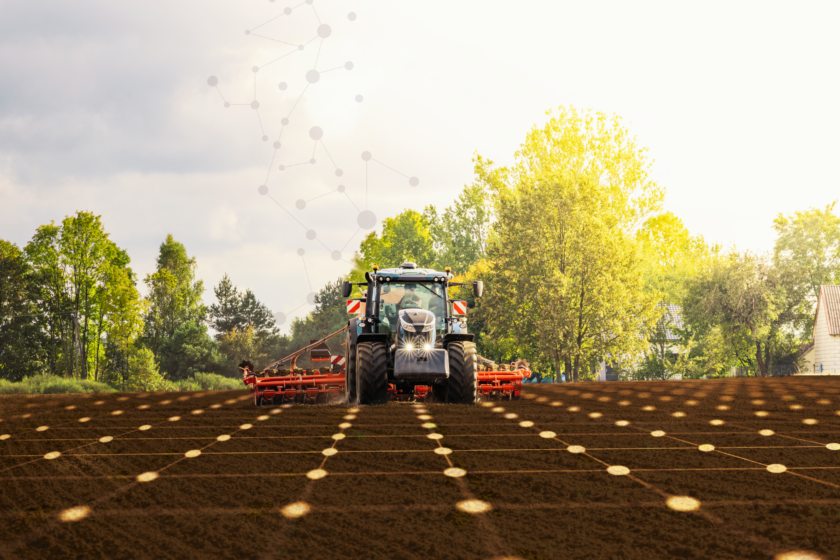
The ever-faster evolution of electronic and information technologies is revolutionizing all production sectors, progressively replacing human labor with robotic and autonomous solutions. This trend is characterized by a pronounced self-accelerating nature, which has now also reached the agricultural mechanization sector. Once dominated by mechanics and hydraulics, this field is increasingly embracing digitalization and informatics.
From Energy Source to Business System
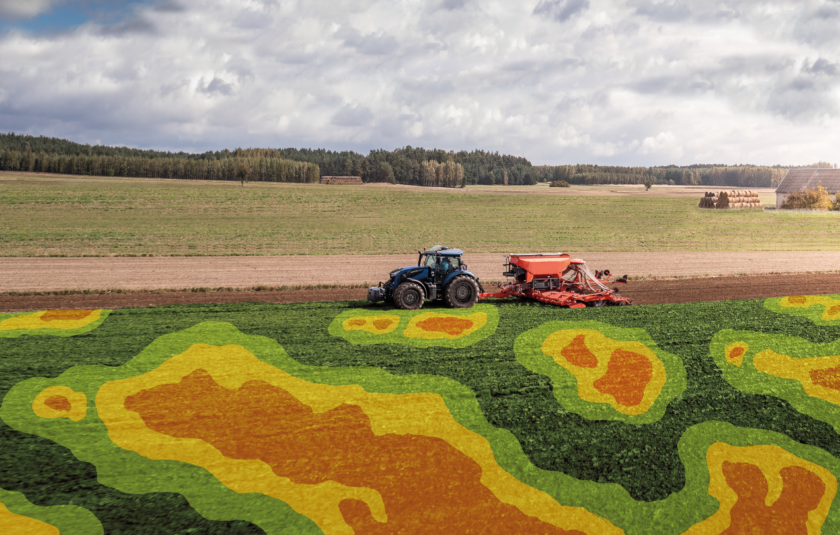
Two technologies are transforming tractors into integrated components of a broader “business system,” where production efficiency can be optimized almost in real-time. An example of this evolution is the “MyLandini” and “MyMcCormick” apps developed by the Argo Tractors Group. These management platforms, installed as standard on most of the Group’s tractors, offer three distinct functionalities called “Fleet Management,” “Remote Diagnostic,” and “Landini/McCormick Farm.”
The foundation of all these solutions is hardware that connects each individual tractor to a remote technical hub, enabling it to monitor not just a single machine but an entire worksite when the tractor communicates with equipment via ISOBUS. This connection operates in real-time, managing a vast amount of data that, once processed, powers the three functionalities mentioned above.
For example, “Fleet Management” uses geographic positioning data to locate and assess the performance of tractors. These insights can optimize the activities of a single worksite or better manage an entire fleet.
Remote Monitoring, Diagnosis, and Interventions
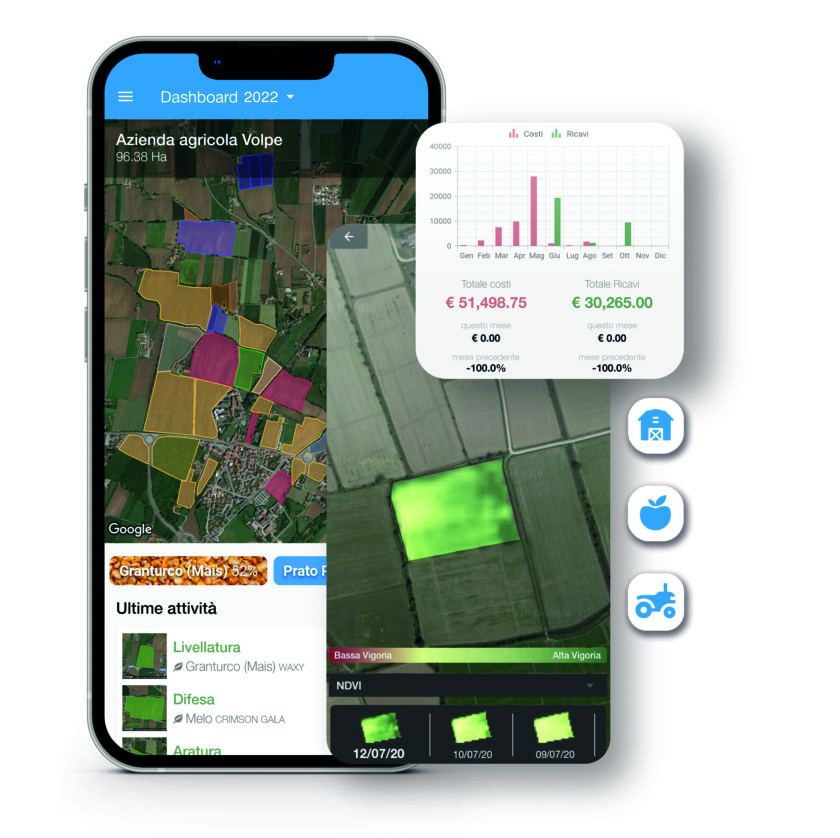
“Remote Diagnostic” also contributes to this goal by supervising the functional state of key components of each machine. If any component operates outside its optimal parameters or design specifications, the platform enables remote checks and diagnostics. In cases of software-related malfunctions or issues that can be resolved remotely, direct interventions are possible.
This system effectively pairs operators with onboard computers that communicate with company or dealership technicians. This ensures swift and informed responses to resolve any problems, minimizing unexpected machine downtimes and enabling predictive maintenance—carried out as needed, rather than at fixed intervals.
The “Landini/McCormick Farm” functionality offers even broader capabilities, allowing operators to manage operational and administrative tasks directly from the tractor. This includes optimizing the application of pesticides and fertilizers based on prescription maps developed over time, as well as automatically updating farm logs. The system also provides access to stock levels of products and all warehouse inventories, including production stocks.
Administration at Your Fingertips
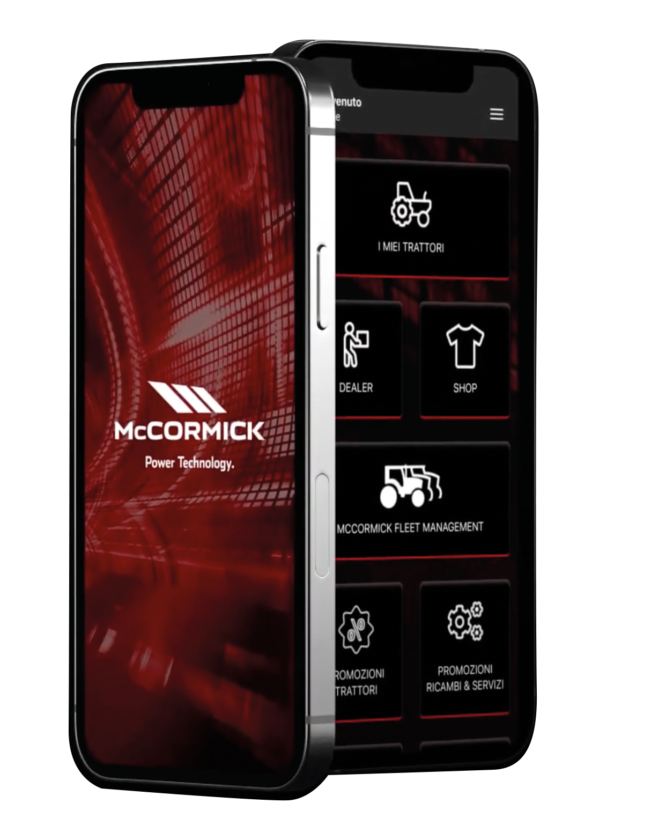
As mentioned, the same software also supports administrative management, enabling tasks like issuing and sending bank transfers or invoices without interrupting fieldwork or immediately afterward. These apps essentially transform the tractor into a mobile office, offering operators a seamless experience enhanced by optional GPS guidance systems.
These GPS systems, available in various configurations, provide precision down to a few centimeters in trajectory, advancement, and distribution management. The most advanced configurations include the “section control” functionality, which regulates applications at field boundaries. Operating alongside the aforementioned functionalities, this system communicates with equipment via ISOBUS to minimize machine and operator hours, reducing maintenance costs and fuel consumption while benefiting the environment by limiting field applications and water usage.
Universal Connectivity
Lastly, the “MyLandini” and “MyMcCormick” apps operate on the global connectivity system “Agrirouter,” which enables communication between equipment from different manufacturers, even those using diverse platforms.
Title: Argo Tractors: Working with the Business in Your Pocket
Translation with ChatGPT